Mit smarter Industry zum smarter Packaging
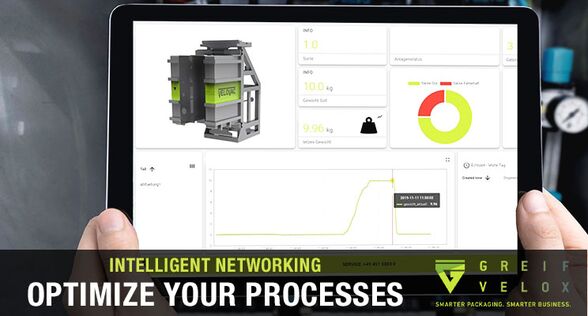
Sinkende Lagerkapazitäten und die auftragsbezogene Individualisierung von Produkten und Produktchargen stellen große Anforderungen sowohl an den Produktions- als auch den Verpackungsprozess. Die Maschinenfabrik Greif-Velox entwickelt daher im Bereich Verpackungsanlagen ganz individuell auf Kundenanforderungen abgestimmte Systeme, die sich dank intelligenter Vernetzung selbst organisieren und Prozesse optimieren. Das bringt deutlich messbare Vorteile für Planung, Produktion, Logistik und Instandhaltung.
Systemmeldungen, aktuelle Gewichte, Anzahl der Säcke, aktuelle Drücke, Drehmomente und mehr – all diese mittels Sensoren gemessenen Maschinenparameter des Abfüllprozesses können dank einer flexiblen Datenschnittstelle in einer Cloud gesammelt werden. Diese kann lokal in dem Greif-Velox Steuerungssystem, dem Kundensystem oder optional auch bei Cloud Services liegen. Über applikationsspezifische IoT-Gateways werden sie mit dem Prozessleit- bzw. Prozesssteuerungssystem des Kunden vernetzt.
Aufrüstung zur Smart Industry für nahezu alle Systeme möglich
„Technische Schnittstellen, die wir zum Beispiel verwenden, sind Standardschnittstellen wie OPC UA oder ProfiNet, mit denen man direkt auf die Daten der speicherprogrammierbaren Steuerung zugreifen kann“, erklärt Benjamin John, Director of Engineering bei Greif-Velox. „Bei der Frage, was für Daten übertragen werden sollen, entwickeln wir ganz individuelle Lösungen für unsere Kunden. Wir reagieren hier sehr flexibel auf die Anforderungen und machen eine Anwendungsberatung – denn meistens ist viel mehr möglich, als die Kunden zuerst denken.“ Auf diese Weise ist es möglich, jedes bestehende System smart-industry-fähig aufzurüsten. So sparen Anwender Kosten bei der Integration, da nicht jede Komponente erneuert werden muss.
Grundlegende Veränderung von Produktions- und Verpackungsprozessen
Der Einsatz sensorisch überwachter, cyber-physikalischer Systeme verändert Produktions- und Verpackungsprozesse grundlegend. Es ist nicht mehr die Auftragsplanung, die zum Beispiel einen Auftrag auf Papier an den Anlagenbediener ausgibt, der schließlich die gewünschten Parameter an der Maschine einstellt. Das Prozessleitsystem entscheidet selbst, welche Abfüllung welches Stoffes in welcher Menge aktuell am optimalsten wäre und gibt die Informationen über das Warenwirtschaftssystem direkt an die Anlage. Möglich ist dies über die zentrale Auswertung der Sensordaten und der Kommunikation zwischen den einzelnen Komponenten, zum Beispiel aus der Vorproduktion, die dem System den Status des Vorprodukts melden. In diesem komplett digitalen Prozess können Stillstandszeiten aufgrund von zeitlich nicht richtig aufeinander abgestimmten Teilprozessen vermieden werden. Ebenso werden Lagerkapazitäten eingespart, wenn der Prozess so auf die Transportlogistik abgestimmt ist, dass das Produkt nach der Produktion direkt abgeholt wird.
Identifikation von Effizienzfressern
Auch während des Abfüllprozesses greift die Anlagensteuerung in den Vorgang ein, um auf Grundlage eines intelligenten Datenverarbeitungsalgorithmus und Informationen aus benachbarten Prozessen die Abläufe zu optimieren. So werden zum Beispiel Soll- und Bruttogewicht permanent abgeglichen. Weicht das Bruttogewicht ab, reagiert die Dosiereinheit unmittelbar und regelt die Abfüllmenge entsprechend nach. Säcke werden so zu jeder Zeit unter verschiedensten Bedingungen optimal befüllt.
„Auf Grundlage der Prozessdaten können wir automatisch darstellen, wie die Effizienz der Anlage ist und wo die Effizienzfresser herkommen“, sagt Benjamin John. Zukünftig können diese Informationen auf einem übersichtlichen Dashboard dargestellt werden, mit dem Anlagenbediener über eine VPN-Verbindung jederzeit ortsunabhängig einen Überblick über die Leistung der Anlage erhalten und auch in den Produktionsprozess eingreifen können. So profitieren Kunden von einem höheren Output und einer Effizienzsteigerung.
Vorteile für das Qualitätsmanagement
Auch für das Qualitäts- und Reklamationsmanagement bieten smart vernetzte Anlagen deutliche Vorteile. „Werden Barcode-Etikettierungen zur Kennzeichnung der Produkte sowie entsprechende Scanner verwendet, können spezifische Gebinde nicht nur identifiziert, sondern auch spezifische Daten über sie gespeichert werden“, sagt Janis Feye, Software-Entwickler bei Greif-Velox. So ist es möglich, das Drehmoment beim Verschluss von Fässern festzuhalten, um nachher den korrekten Verschlussvorgang nachweisen zu können. Wird eine bestimmte Charge eines Produkts reklamiert, kann über die Analyse der Daten der Produktionszeitraum und die Ursache des Problems schneller identifiziert und nachhaltig behoben werden. Das senkt die Reklamationskosten und erhöht die Reputation der Hersteller bei ihren Kunden hinsichtlich der Qualität des Produkts.
Fortschritte in der Predictive Maintenance
Um die Maschinenleistung und die Effizienz weiter zu erhöhen, entwickelt das Greif-Velox-Team außerdem Modelle, um die gesammelten Prozessdaten für die Predictive Maintenance, also die proaktive Wartung, zu nutzen. „Dafür werden zeit-, zyklus- und zustandsbasierte Daten zusammengetragen und ausgewertet“, erklärt Benjamin John. Auf diese Weise kann das System den Anwender rechtzeitig vor einem möglichen Ausfall informieren, wenn eine Anlagenkomponente ausgetauscht werden muss. Indikatoren dafür können unter anderem die Einsatzdauer sein, aber auch verschlechterte Leistungsdaten. Mit der rechtzeitigen Wartung können ebenfalls Ausfälle und Stillstandszeiten im Produktionsprozess minimiert werden. Das bedeutet, dass die Auslastung der Maschinen optimiert wird, was insgesamt zu einer Steigerung der Produktivität führt.
So verfolgt Greif-Velox mit den IoT-Entwicklungen im Bereich Verpackungsanlagen eine kontinuierliche Verbesserung hinsichtlich der Flexibilität, Autonomie, Leistungsfähigkeit, Verfügbarkeit und Transparenz entlang der Wertschöpfungskette.