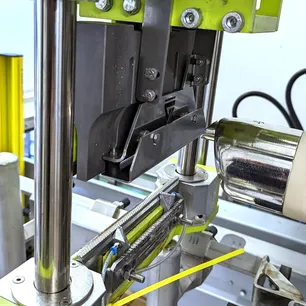
Produktdaten ValvoDetect
Gebinde | Ventilsäcke aus Papier, PE, PP |
---|---|
Branche | Chemie, Lebensmittel |
Passende Anlagen | BVP- und BVPV- Luftpackersysteme |
Zubehör & Erweiterung | SmartValvoCut, ValvoSeal, ValvoMat |
ValvoDetect: Die Innovation für saubere Säcke und Paletten
Die weltweit einzigartige Lösung für saubere Säcke und Paletten
Zusätzliche Reinigungs- und Wartungskosten durch kontaminierte Produktionslinien
ValvoDetect minimiert Produktverlust und reduziert die Reinigungskosten durch präzise Fehlererkennung und -eliminierung.
Hohe Reklamationsraten und Kundenunzufriedenheit durch fehlerhafte Ventilsack-Verschweißungen
Durch ValvoDetect werden fehlerhafte Säcke frühzeitig erkannt und aussortiert, was die Produktqualität sichert und die Kundenzufriedenheit erhöht.
Teurer Zeitverlust durch manuelle Qualitätskontrollen und Nachbearbeitungen
Automatisierte Prüfprozesse des ValvoDetect steigern die Effizienz und Durchlaufzeit der Produktion.
Häufige Produktionsunterbrechungen und Stillstandszeiten durch manuelle Fehlerkorrekturen
ValvoDetect reduziert Stillstandzeiten durch automatisierte Fehlererkennung und -behebung, was die Produktionsstabilität erhöht.
Als Teil eines geschlossenen Produktionssystems gehen unsere Abfüllanlagen weit über die reine Abfüllfunktion hinaus: Sie bilden einen integralen Teil eines Gesamtsystems, das sich nahtlos in bestehende Produktionslinien einfügt und diese ergänzt.
Unsere Full-Line-Anlagen sind in der Lage, komplexe Anforderungen von der Gebindebereitstellung über die Abfüllung bis hin zur Nachbearbeitung und Lagerung zu bedienen, was uns zu einem ganzheitlichen Systemanbieter in der Produktionstechnik macht. Dabei steht die individuelle Anpassung im Vordergrund, um eine optimale Integration in die jeweiligen Betriebsabläufe zu gewährleisten.

Mit Standardlösungen sparen Sie Geld.
Mit individuellen Lösungen verdienen Sie Geld.
Unsere Philosophie bei Greif-Velox ist es, individuell zugeschnittene Lösungen statt Standardprodukte zu bieten.
Jede Abfüllanlage wird genau auf die Bedürfnisse und Prozesse unserer Kunden abgestimmt, um eine schnelle Integration in bestehende Produktlinien oder die Entwicklung einer vollständig abgestimmten Full-Line-Anlage zu ermöglichen.
Wir legen großen Wert auf Präzision, Sicherheit und Automatisierung, um die Produktionseffizienz unserer Kunden bei maximaler Flexibilität zu steigern.
ValvoDetect für die Chemie- und Lebensmittel-Branche
Innovative Feststoff-Abfüllanlage mit ValvoDetect für ICL Ladenburg
Die Feststoff-Abfüllanlage von GREIF-VELOX bei ICL Ladenburg führte zu einer signifikanten Senkung der Reklamations- und Reinigungskosten, die ursprünglich durch fehlerhaft verschweißte Säcke verursacht wurden. Diese Kostenproblematik, die jährlich mindestens 20.000 Euro betrug, wurde durch die Einführung des ValvoDetect am Luftpacker BVP radikal verbessert. ValvoDetect sorgt mit seinen optischen Sensoren dafür, dass nur korrekt positionierte Säcke verschweißt werden, indem es fehlerhaft aufgesteckte Säcke vor dem Verschweißen erkennt und aussortiert.
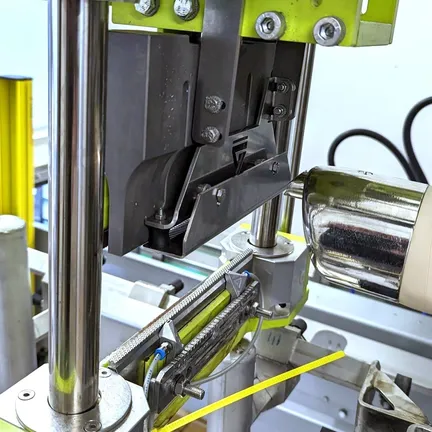
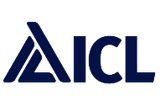
Finden Sie den richtigen Ansprechpartner
Direkter Kontakt zu GREIF-VELOX oder kompetenter Handelspartner bei Ihnen vor Ort:
Hier finden Sie den richtigen Ansprechpartner für Ihr Anliegen.
Passende GREIF-VELOX-Anlagen zur Ventilsack-Abfüllung
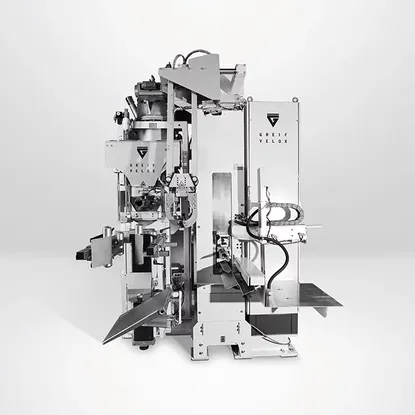
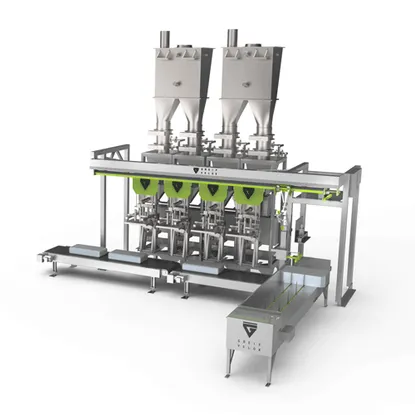
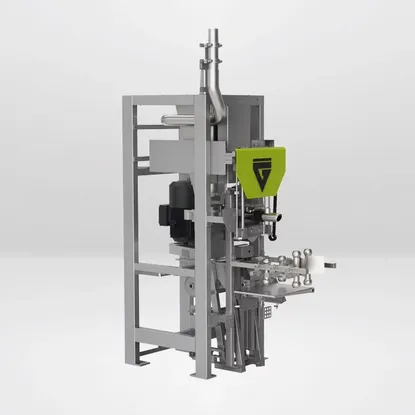