GREIF-VELOX transformiert die Produktionstechnik
Unsere hochautomatisierten Abfüll- und Verpackungsanlagen überwinden die Produktionshürden großer und weltweit aktiver Unternehmen
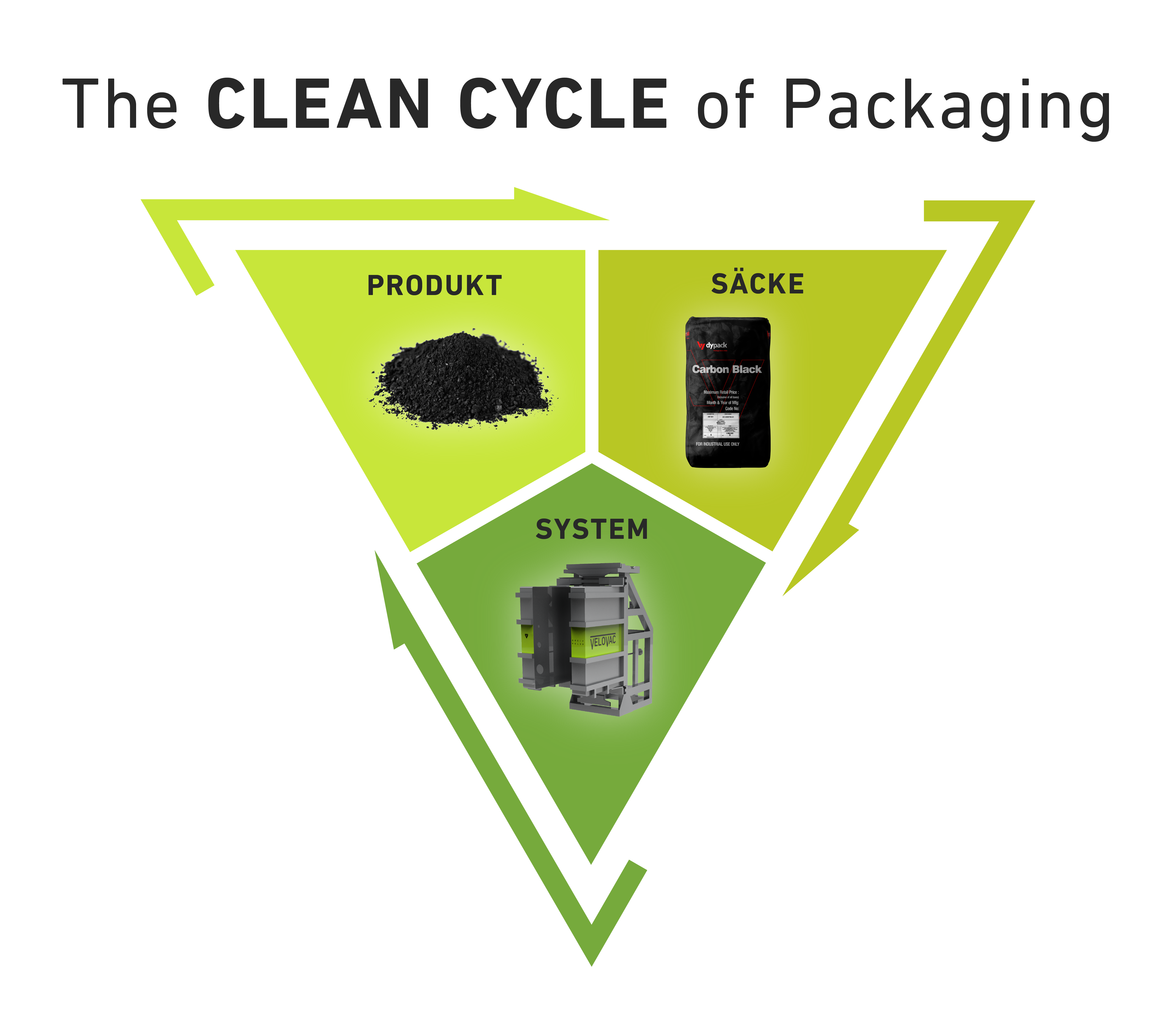
Flexibler
Unsere modularen Abfüllanlagen ermöglichen eine schnelle Anpassung an unterschiedliche Produktarten und Gebindegrößen, was eine nahtlose Umstellung zwischen verschiedenen Produktionslinien und eine erhebliche Reduzierung der Umrüstzeiten ermöglicht.
Nachhaltiger
Durch die Einführung energieeffizienter Systeme und nachhaltiger Produktionsprozesse reduzieren unsere Anlagen den CO2-Fußabdruck und fördern die Wiederverwendbarkeit von Ressourcen, was in unseren neuesten Anlagenkonzeptionen verankert ist.
Effizienter
Mit innovativer Abfülltechnik erhöhen wir Abfüllgeschwindigkeiten um bis zu 50 Prozent oder verdoppeln die Ausstoßkapazität von Säcken pro Stunde.
Sauberer
Durch die Anwendung unserer VeloVac-Technologie ermöglichen wir staubfreie Absackprozesse, die nicht nur die Arbeitsumgebung verbessern, sondern auch die Umweltbelastung deutlich reduzieren.
Sicherer
Unsere speziell entwickelten Sicherheits- und Reinigungsfunktionen und fortschrittlichen Kontaminationsschutz-Maßnahmen erhöhen die Sicherheit am Arbeitsplatz um ein Vielfaches und setzen neue Standards in der Produktionshygiene.
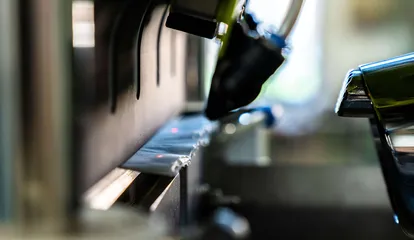
Fallstudie:
ICL Ladenburg
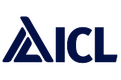
Signifikante Reduzierung von Reklamations- und Reinigungskosten Verbesserung der Endkunden-Zufriedenheit und Markenreputation.
ICL Ladenburg gehört zur Lebensmittel- und Chemiebranche. Das Unternehmen betreibt Produktionsanlagen für Lebensmittel und Getränke sowie für technische Anwendungen und entwickelt, produziert und vertreibt Additive für die Nahrungsmittelindustrie und industrielle Anwendungen, darunter Zusätze für die Reinigungsmittelherstellung, die Metalloberflächenbehandlung, technische Additive für Lacke und Farben sowie für die Kosmetikund Bauindustrie.
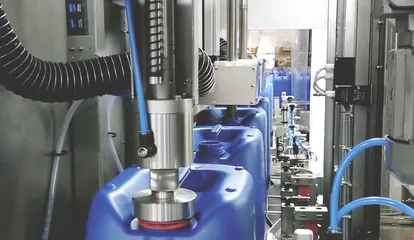
Fallstudie:
Evonik
Steigerung der Abfüllgeschwindigkeit um 50 Prozent Verbesserung der Produktsicherheit durch fortschrittliche Kontaminationsschutzmaßnahmen.
Evonik gehört zur Spezialchemiebranche. Sein Produktportfolio erstreckt sich von hochleistungsfähigen Materialien bis hin zu Additiven für diverse Industrien, darunter Wasserstoffperoxid, ein wesentlicher Bestandteil in den Bereichen Bleichmittelherstellung und Desinfektion.
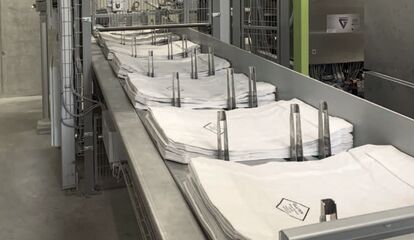
Fallstudie:
GoodMills Deutschland
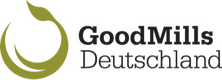
Verdopplung der Verpackungseffizienz und der Produktionsleistung auf bis zu 400 Säcke pro Stunde. Minimierung von Reinigungsaufwand und Umrüstzeit.
GoodMills Deutschland gehört zur Lebensmittelbranche und zählt zu den führenden Mühlenunternehmen in Europa. Spezialisiert auf die Herstellung hochwertiger Mehle und Grieße für Bäckereien, Lebensmittelverarbeiter und die Getränkeindustrie, legt GoodMills besonderen Wert auf Produktqualität, Effizienz und Nachhaltigkeit in seinen Produktionsprozessen.
Erfolgsfaktor: Projektabwicklung Anlagenentwicklung
Jedes Projekt eine individuelle Lösung nach standardisiertem Prozess
Wir setzen das Stage-Gate-Modell ein, um Ihnen eine strukturierte und effiziente Projektabwicklung zu garantieren. Bei diesem Ansatz wird jedes Projekt durch klar definierte Stufen (Gates) geführt, die entscheidend sind, um maßgeschneiderte Lösungen systematisch zu entwickeln und zu validieren. Durch die Anwendung standardisierter Prozesse innerhalb des Stage-Gate-Rahmens sichern wir nicht nur die Qualität und Effizienz jeder Anlage, sondern sorgen auch für Transparenz und Nachvollziehbarkeit in jeder Projektphase.
Konzeptphase
Zu Beginn setzen wir uns intensiv mit Ihren spezifischen Anforderungen auseinander, um ein fundiertes Verständnis für Ihre Produktionsziele zu entwickeln. Das von uns erstellte Konzept basiert auf Ihrem Lastenheft und beinhaltet ein optimales Anlagenlayout, effiziente Abläufe und ein durchdachtes Sicherheitskonzept.
Design-Phase
Nach Konzeptfreigabe transformieren wir Ihre Anforderungen in ein detailliertes 3D-Anlagendesign. Unser Engineering-Team nutzt fortschrittliche CAD-Tools – und auf Wunsch 3D-Scans Ihres Standorts –, um sicherzustellen, dass jede Komponente der Anlage präzise Ihren Anforderungen entspricht.
Produktionsphase
Mit einer ausgeprägten Fertigungstiefe geht Greif-Velox über standardisierte Lösungen hinaus, um individuelle Kundenwünsche zu erfüllen. Jede Baugruppe unterzieht sich strengen Qualitätsprüfungen, um eine durchgängig hohe Fertigungsqualität sicherzustellen – von der Beschaffung bis zur finalen Montage.
WIBN-Phase (Werksinbetriebnahme)
In dieser Phase kommt Ihre Anlage bei Greif-Velox zum ersten Mal vollständig zum Einsatz. Durch eingehende Tests und Optimierungen garantieren wir, dass alle Funktionen reibungslos arbeiten. Der interne Factory Acceptance Test (IFAT), gefolgt vom Factory Acceptance Test (FAT) mit Ihnen, leitet die erfolgreiche Übergabe in die Montagephase ein.
Montagephase
Nach der detaillierten Planung und Fertigung liefern wir die Anlage an Ihren Standort und führt die professionelle Montage sowie Inbetriebnahme durch. Abgerundet wird dieser Abschnitt durch den Site Acceptance Test (SAT), der den reibungslosen Start Ihrer Produktion bestätigt.
Service-Phase
Greif-Velox unterstützt Sie auch nach der Inbetriebnahme kontinuierlich mit umfassenden Serviceleistungen. Unser Ziel ist es, die Langlebigkeit und hohe Leistung Ihrer Anlage zu sichern, damit Sie dauerhaft von maximaler Produktivität und Effizienz profitieren.
Zertifizierte Qualität. Nachhaltige Verantwortung.
Als zertifiziertes Unternehmen nach ISO 9001:2015 und ISO 14001:2015 steht GREIF-VELOX für verlässliche Qualität und verantwortungsvolles Handeln. Unsere internen Prozesse sind konsequent auf Effizienz, Sicherheit und Kundenzufriedenheit ausgerichtet – geprüft durch unabhängige Audits.
Gleichzeitig übernehmen wir Verantwortung für die Umwelt: Unser zertifiziertes Umweltmanagementsystem stellt sicher, dass wir Ressourcen schonen, Emissionen minimieren und nachhaltige Lösungen in der Verpackungstechnologie entwickeln.
Firmenstruktur & Märkte
Weltweites Business. Weltweiter Service. In mehr als 89 Ländern.
4 Schlüsselabteilungen
im Firmensitz Lübeck
Administration & Koordination
Im Herzen unserer Abläufe in Lübeck liegt die Administration, das Rückgrat von Greif-Velox, das alle Backoffice-Aktivitäten und die gesamte Koordination der verschiedenen Einheiten umfasst. Unter der Leitung der Geschäftsführung sorgt dieser Bereich für eine effiziente Verbindung zwischen den Abteilungen wie HR und Finanzen und den operativen Einheiten wie Service und Realisation.
Durch die Implementierung modernster Collaboration-Tools wird sichergestellt, dass alle Projekte effizient erfasst, dokumentiert und mit höchster Transparenz geplant werden, was unseren Kunden eine klare und nachvollziehbare Einsicht in die Projektabwicklung bietet.
Vertrieb & Beratung
Unsere Vertriebsingenieure sind mehr als nur die Erstansprechpartner für unsere Kunden; sie sind Experten, die Ihnen von der ersten Anfrage bis zur finalen Umsetzung zur Seite stehen.
Spezialisiert auf Leichtstoff-,Feststoff- und Flüssigkeitsabfüllung bieten sie umfassende Beratungen an und konzipieren mit Unterstützung unseres Teams für Innovation & Anwendung individuelle Anlagenlösungen, die nicht nur auf Ihre spezifischen Bedürfnisse zugeschnitten sind, sondern Ihnen auch signifikante Marktvorteile verschaffen. Unsere Ingenieure setzen auf die Entwicklung maßgeschneiderter, zukunftsweisender Lösungen, die Ihren Betrieb effizienter und profitabler machen.
Service & Installation
Das Service-Team von Greif-Velox vereint technisches Know-how in Mechanik, Elektronik und Software, um eine breite Palette von Kundenanforderungen direkt zu erfüllen. Von der ersten Konzeptphase an beteiligt kennen unsere Techniker jedes Detail Ihres Projekts, was eine effiziente und sachkundige Installation sowie eine umfassende Betreuung sicherstellt.
Mit den neuesten Service-Tools und Technologien, einschließlich fortschrittlicher VPN-Lösungen, ermöglicht unser Team nicht nur eine optimale Inbetriebnahme, sondern unterstützt Sie auch langfristig bei Upgrades, Optimierungen und im Ersatzteilmanagement.
Konstruktion & Realisation
In dieser Abteilung arbeiten unsere Ingenieure und Konstrukteure Hand in Hand, um präzise und effektive Abfülllösungen zu entwickeln. In enger Zusammenarbeit mit der Abteilung für Innovation & Anwendung entstehen hier individuelle und innovative Lösungen, die die Standards der Branche neu definieren.
Unser Projektmanagement-Team garantiert einen transparenten und effizienten Prozess von der Planung bis zur endgültigen Realisierung, wobei der Schwerpunkt auf minimalen Aufwendungen für unsere Kunden liegt und gleichzeitig höchste Qualitätsstandards eingehalten werden.
Service bieten wir Ihnen jeden Tag.
verarbeiten wir jährlich.
beliefern wir bisher. Tendenz steigend.
Dieser Anteil unserer Kunden fragt künftige Projekte stets bei uns an.
beschäftigen wir weltweit bei Greif-Velox.
haben wir bisher realisiert.
und Stücklisten befinden sich in unserem ERP-System.
Kann unsere Jahresproduktion an Luftverpackern absacken.
Von der Greifen-Mühle zum Marktführer
1000 Jahre Firmengeschichte
1100
Mönche gründen die Greifen-Mühle in Klützow.
1399
Verkauf der Mühle und des Dorfs an den Priester v. d. Zinne zugunsten einer geistlichen Stiftung.
1409
Allmählicher Übergang der Mühle in das Privatvermögen der Familie v. d. Zinne.
1734
Johann Mahlkuch betreibt die Mühle und erweitert sie im Laufe der Jahre.
1852
Ausbau der Mühle nach dem innovativen "amerikanischen System" zur Herstellung von sehr feinem, teurerem Mehl.
1865
Umbau und technische Erweiterung der Mühle um Turbinen und Dampfmaschinen.
1891
Die Mühle brennt durch ein heißgelaufenes hölzernes Wellenlager ab und wird unmittelbar danach mit neuen Maschinen komplett neu aufgebaut.
1908
Ernst Mahlkuch, Besitzer der Mühle, lässt sich im Jahr seiner Meisterprüfung die erste eichfähige automatische Absackwaage patentieren.
1914
Wegen des beginnenden Ersten Weltkriegs muss die Mühle sechs Pferde und mehrere Mitarbeiter abgeben. Sie schließt sich außerdem gewinnbringend der neu gegründeten Reichsgetreidestelle an.
1920
Intensiver Ausbau von Mühle und Mühlspeicher sowie Anschaffung elektrischer Limousinen.
1921
Neue Patentanmeldungen für eine automatische Sackpackwaage und einen Sackaufzug.
1934
Vollständiger Neubau der Mühle wegen eines Großbrandes im Jahr 1933. Mit diversen Neuerungen und Innovationen durch den Besitzer, Erfinder Ernst Mahlkuch.
1938
Nach der Anmeldung mehrerer Patente in der Waagen- und Absacktechnologie wird in Klützow das Greif-Werk gegründet und gebaut.
1941
Das Greif-Werk wird wegen der großen Nachfrage an dessen Absackmaschinen stark ausgebaut.
1945
Gründung der Greif-Werke in Lübeck.
1978
Übernahme durch die Möllers Group.
1997
Umfirmierung der Greif-Werke in Greif-Velox.
1999
Übernahme der Firma Logdos (Flüssigabfüllung).
2012
Greif-Velox produziert hochwertige, individuelle Full-Line-Anlagen.
2018
Das Greif-Velox-Management-Team übernimmt gemeinsam mit der Beteiligungsfirma BPE alle Anteile des Unternehmens.
News & Publikationen
Bestens informiert und auf dem neuesten Stand
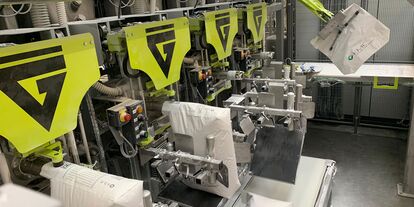
Erkennen und Aussortieren fehlerhafter Säcke mit ValvoDetect.
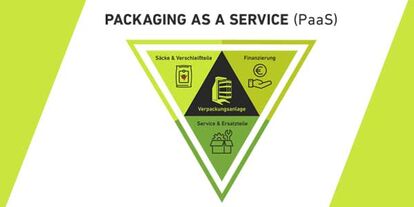
Maximale Effizienz, volle Kostenkontrolle und zuverlässige Versorgung: Mit unserem neuen PaaS-Modell machen wir industrielle Pulverabsackung einfacher denn je.
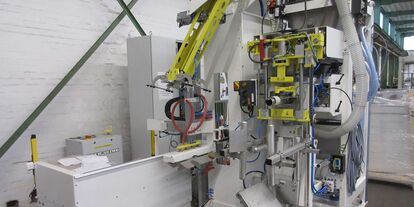
Effiziente Abfüllung von mikronisierten Wachsen mit unserem Brutto-Pneumatikpacker.
Karriere bei Greif-Velox
Sie suchen einen Job, in dem Sie sich verwirklichen können und Ihre Fähigkeiten voll zum Einsatz kommen? Dann haben wir den richtigen Arbeitsplatz für Sie! Wir bei Greif-Velox sind Visionäre, Partner, Lehrende und Lernende – und natürlich auch ein unschlagbares Team. Wir arbeiten jeden Tag daran, neben bahnbrechenden Absackmaschinen und Abfüllanlagen eine positive Arbeitsatmosphäre zu schaffen – zum Beispiel durch flexible Arbeitszeitmodelle, attraktives Gehalt und Mitarbeiterevents. Denn wir wissen: Nur wer gern in seinem Team arbeitet, kann sein Potenzial voll ausschöpfen.
Wir sind ein Unternehmen mit 1000-jähriger Geschichte, das konsequent nach vorn blickt: Neben Effizienz und Zuverlässigkeit, gehört ganz klar Innovation zu den Werten, die uns vorantreiben. Ob im technischen oder kaufmännischen Bereich oder als Azubi – seien Sie mit dabei! Starten Sie jetzt Ihre Karriere bei Greif-Velox.
Und sollte Ihre Stelle hier gerade nicht zu finden sein, freuen wir uns über Ihre Initiativbewerbung.
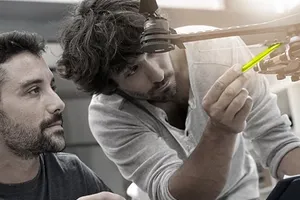
Technische Berufe
Vom Elektroniker und Ingenieur bis hin zum IT-Experten – hier finden Sie die Stellenausschreibungen im technischen Bereich.
mehr erfahren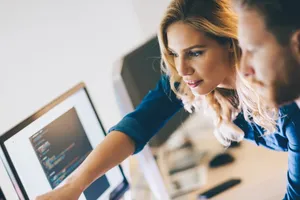
Kaufmännische Berufe
Von Büromanagement über Controlling bis zur Sachbearbeitung: Unsere kaufmännischen Jobs sind hier.
mehr erfahren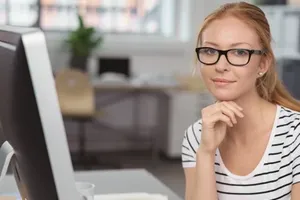
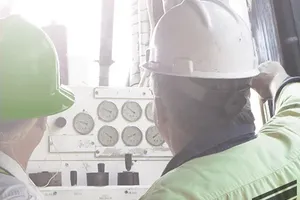
Initiativbewerbung
Die passende Ausschreibung noch nicht gefunden? Bewerben Sie sich bei uns initiativ!
mehr erfahren