Predictive Maintenance: Produktionsoptimierung durch präventive Anlagenwartung
Produktionsausfälle gehören zu den teuersten und zugleich vermeidbarsten Risiken im industriellen Umfeld. Ungeplante Stillstandzeiten führen nicht nur zu direkten Umsatzeinbußen, sondern beeinträchtigen auch Liefertermintreue, Kundenbeziehungen und letztlich die Wettbewerbsfähigkeit des gesamten Unternehmens. Interne Analysen und unabhängige Studien zeigen, dass selbst kurze Ausfallzeiten enorme Kosten verursachen – insbesondere, wenn Prozesse hoch automatisiert sind und als Engpass im Wertstrom fungieren.
Traditionelle Wartungs- und Instandhaltungskonzepte, wie rein reaktive oder zeitbasierte Instandhaltung, stoßen angesichts steigender Anlagenkomplexität und Digitalisierung an ihre Grenzen. Unvorhersehbare Fehler, aufwändige Fehlersuche und lange Reaktionszeiten beim Service verursachen nicht selten Kosten in sechsstelliger Höhe pro Jahr und Anlage. Gleichzeitig wächst der Druck, Anlagenverfügbarkeit, Produktqualität und Ressourceneffizienz kontinuierlich zu steigern – ohne Mehraufwand für Personal und Budget.
In diesem Spannungsfeld etabliert sich Predictive Maintenance als zentraler Hebel für eine zukunftsorientierte Instandhaltungsstrategie. Durch intelligente Überwachung, datenbasierte Analyse und automatisierte Frühwarnsysteme lassen sich potenzielle Ausfälle nicht nur frühzeitig erkennen, sondern auch gezielt vermeiden. Predictive Maintenance schafft damit die Voraussetzung, Wartungsfenster optimal zu planen, ungeplante Stillstände drastisch zu reduzieren und die Lebensdauer von Maschinen entscheidend zu verlängern.
Greif-Velox greift diese Herausforderungen mit innovativen, praxisbewährten Lösungen auf. Mit digitalen Werkzeugen wie VeloGuard integriert Greif-Velox Predictive-Maintenance-Prinzipien direkt in die eigene Anlagenwelt – und schafft so einen messbaren Mehrwert für Produktionsunternehmen, die maximale Anlagenverfügbarkeit, höchste Prozesssicherheit und planbare Instandhaltung anstreben. Wie dieser Ansatz konkret funktioniert und welche Vorteile Predictive Maintenance im Zusammenspiel mit Greif-Velox-Anlagen bietet, erfahren Sie im weiteren Verlauf dieses Artikels.
Was ist Predictive Maintenance?
Predictive Maintenance – die vorausschauende Instandhaltung – beschreibt eine Wartungsstrategie, bei der Ausfälle und Verschleiß nicht mehr nur reaktiv oder nach festen Intervallen behandelt werden, sondern gezielt durch kontinuierliche Überwachung und datenbasierte Analyse vorab erkannt und verhindert werden. Ziel ist es, die tatsächliche Nutzung und den aktuellen Zustand der Maschine in Echtzeit zu bewerten, um den optimalen Wartungszeitpunkt exakt vorherzusagen.
Abgrenzung zu klassischen Wartungskonzepten:
Im Vergleich zur reaktiven Wartung, bei der ausschließlich im Störungsfall gehandelt wird, und zur präventiven Wartung, die auf festen Wartungsintervallen basiert, ermöglicht Predictive Maintenance einen maximalen Grad an Planungssicherheit und Ressourceneffizienz. Während reaktive Ansätze zu ungeplanten Stillständen und Folgeschäden führen können, verursachen präventive Methoden häufig unnötige Wartungsarbeiten und damit verbundene Kosten. Predictive Maintenance verbindet das Beste aus beiden Welten: Instandhaltung findet dann statt, wenn sie tatsächlich notwendig und wirtschaftlich sinnvoll ist.
Kernelemente: Condition Monitoring, Datenanalyse, KI
Im Zentrum von Predictive Maintenance steht das Condition Monitoring – also die permanente Zustandsüberwachung relevanter Komponenten und Prozesse. Sensoren erfassen Betriebsparameter wie Temperatur, Druck, Vibration, Laufzeiten oder Schaltzyklen in Echtzeit. Die dabei entstehenden Daten werden mittels moderner Analyseverfahren ausgewertet, um Trends und Abweichungen frühzeitig zu erkennen.
Moderne Predictive-Maintenance-Systeme nutzen fortschrittliche Algorithmen und zunehmend auch Künstliche Intelligenz (KI), um komplexe Zusammenhänge zwischen Prozessparametern und potenziellen Ausfallursachen zu identifizieren. So entstehen digitale Frühwarnsysteme, die eine präzise Prognose der verbleibenden Restlebensdauer (Remaining Useful Life, RUL) von Bauteilen oder Anlagen ermöglichen und Wartungsbedarf automatisiert melden.
Technische Voraussetzungen für Predictive Maintenance
Für die Umsetzung von Predictive Maintenance sind verschiedene technische Voraussetzungen zu erfüllen:
- Sensorik und Automatisierung: Die Anlage muss mit geeigneten Sensoren für die Überwachung aller relevanten Komponenten ausgestattet sein.
- Dateninfrastruktur: Eine sichere, schnelle Erfassung, Speicherung und Übertragung von Sensordaten – oft in Echtzeit – ist die Basis für jede Analyse.
- Analyse- und Auswertungssoftware: Algorithmen, KI-Tools oder spezielle Softwarelösungen werten die Daten automatisiert aus und leiten Handlungsempfehlungen ab.
- Integration ins Bedien- und Wartungssystem: Idealerweise werden die Zustandsdaten und Wartungsempfehlungen direkt ins HMI (Human Machine Interface) und die bestehende Wartungsorganisation integriert, sodass Verantwortliche jederzeit den Überblick behalten.
Mit dieser Infrastruktur lassen sich Maschinen und Anlagen nicht nur effizienter betreiben, sondern ungeplante Ausfälle nahezu ausschließen. Greif-Velox nutzt diese Prinzipien konsequent in der eigenen Produktwelt – unter anderem mit dem Condition-Monitoring-System VeloGuard.
Historische Entwicklung von „Breakdown Maintenance“ bis „Predictive Maintenance“
Die Instandhaltung in der industriellen Produktion hat in den letzten Jahrzehnten einen fundamentalen Wandel durchlaufen. Ursprünglich dominierten rein reaktive Ansätze: Maschinen und Anlagen wurden erst dann gewartet, wenn bereits ein Defekt oder Ausfall eingetreten war (Breakdown Maintenance). Diese Strategie führte häufig zu langen Stillstandszeiten, unplanbaren Kosten und reduziertem Output.
Mit zunehmender Automatisierung und steigendem Kostendruck folgte die Etablierung der vorbeugenden Wartung (Preventive Maintenance). Hierbei erfolgten Wartungen in festen Intervallen, unabhängig vom tatsächlichen Zustand der Maschine. Zwar konnten so viele Ausfälle verhindert werden, doch zeigte sich schnell: Unnötige Wartungsarbeiten und der Austausch noch intakter Komponenten führten zu ineffizienter Ressourcennutzung und vermeidbaren Kosten.
Die konsequente Weiterentwicklung dieses Ansatzes ist die zustandsorientierte und vorausschauende Wartung (Condition-based & Predictive Maintenance). Mithilfe moderner Sensorik, Digitalisierung und intelligenter Datenanalyse wird der aktuelle Zustand aller kritischen Komponenten permanent überwacht. Predictive Maintenance ermöglicht es, Wartungsbedarf exakt vorherzusagen und Instandhaltungsmaßnahmen optimal zu planen – und reduziert so ungeplante Stillstände sowie Kosten nachhaltig.
Bedeutung von Total Productive Maintenance (TPM) als strategische Basis
Total Productive Maintenance (TPM) gilt als wegweisende Philosophie für eine effiziente und nachhaltige Instandhaltung im Industrieumfeld. TPM verbindet operative Exzellenz mit einer unternehmensweiten Beteiligung – von der Werksleitung bis zum Anlagenbediener. Ziel ist es, sämtliche Verlustquellen zu eliminieren, die Anlagenverfügbarkeit zu maximieren und die Produktivität durch kontinuierliche Verbesserung systematisch zu steigern.
Die acht TPM-Säulen – von der autonomen Wartung (Jishu Hozen) über fokussierte Verbesserungen (Kaizen), geplante Wartung, Qualitäts-, Schulungs- und Sicherheitsmanagement bis hin zur entwicklungsbegleitenden Instandhaltung – bieten den organisatorischen Rahmen, auf dem auch moderne Predictive-Maintenance-Konzepte aufbauen. Erst die Kombination von TPM-Prinzipien mit datenbasierter Predictive Maintenance erschließt das volle Potenzial digitaler Instandhaltungsstrategien.
Wandel der Erfolgsfaktoren: Von reaktiver zu proaktiver Instandhaltung
Der Wandel von reaktiver zu proaktiver Instandhaltung ist geprägt vom technologischen Fortschritt und einem veränderten Rollenverständnis in der Produktion. Während in klassischen Strukturen Wartung als „notwendiges Übel“ betrachtet wurde, rücken heute Anlagenverfügbarkeit, Ressourceneffizienz und Prozesssicherheit in den Fokus der Wertschöpfung. Predictive Maintenance baut auf den Lehren des TPM auf und nutzt moderne Technologien, um das Ziel der verlustfreien Produktion greifbar zu machen.
Unternehmen, die diesen Paradigmenwechsel frühzeitig vollziehen und ihre Instandhaltungsstrategie mit TPM und Predictive-Maintenance-Prinzipien verknüpfen, sichern sich nachhaltige Wettbewerbsvorteile – durch höhere Anlagenverfügbarkeit, reduzierte Wartungskosten und einen messbaren Zuwachs an Produktivität.
Wirtschaftliche Effekte: Weniger Stillstände, geringere Kosten, höhere OEE
Predictive Maintenance entfaltet ihren wirtschaftlichen Nutzen insbesondere durch die drastische Reduktion ungeplanter Stillstandszeiten. Je besser Ausfälle prognostiziert und vermieden werden, desto höher fällt die Anlagenverfügbarkeit aus – ein zentraler Treiber für die Produktivität (Overall Equipment Effectiveness, OEE) und für die Wettbewerbsfähigkeit des Unternehmens.
Durch die kontinuierliche Überwachung und automatische Diagnose lassen sich bis zu 90 % der Ausfallzeiten vermeiden. Praxisbeispiele – wie das Mineralmahlwerk Hamm, das die VeloGuard Selbsttest-Funktion von Greif-Velox einsetzt – belegen: Die Wartungskosten konnten um bis zu 80 % reduziert werden, ungeplante Produktionsausfälle nahezu vollständig entfallen.
Höhere Maschinenverfügbarkeit und verlängerte Lebensdauer
Indem Predictive Maintenance Verschleiß frühzeitig erkennt und Wartungen gezielt ansetzt, bleiben Maschinen dauerhaft im optimalen Betriebszustand. Das führt nicht nur zu einer konstant hohen Anlagenverfügbarkeit, sondern verlängert auch die Lebensdauer kritischer Komponenten und der gesamten Anlage erheblich. Teure Notfallreparaturen und Folgeschäden durch Folgedefekte werden verhindert, Wartungsbudgets lassen sich effizienter steuern.
Verbesserte Planung von Wartungsfenstern
Ein weiterer entscheidender Vorteil ist die Möglichkeit, Wartungsmaßnahmen vorausschauend und produktionstaktisch zu planen. Geplante Wartungsfenster lassen sich optimal in Produktionszyklen integrieren, wodurch notwendige Eingriffe in Nebenzeiten oder planbare Stillstände verschoben werden können. Dadurch sinkt der Anteil ungeplanter Ausfälle und teurer Ad-hoc-Einsätze auf ein Minimum. Unternehmen gewinnen die volle Kontrolle über ihre Instandhaltungsprozesse und erhöhen ihre Liefertreue.
Steigerung der Arbeitssicherheit
Predictive Maintenance trägt maßgeblich zur Arbeitssicherheit bei: Regelmäßige, zustandsbasierte Prüfungen und der rechtzeitige Austausch sicherheitsrelevanter Komponenten minimieren das Risiko von Unfällen und gefährlichen Betriebszuständen. Darüber hinaus ermöglicht die automatisierte Fehlererkennung auch weniger erfahrenen Mitarbeitenden, Wartungsbedarf frühzeitig zu erkennen und korrekt zu handeln – die Sicherheit im Produktionsumfeld wird auf ein neues Niveau gehoben.
Herausforderungen typischer Produktionsbetriebe
Produktionsunternehmen im Mittelstand stehen unter hohem Effizienzdruck. Besonders bei automatisierten Anlagen führen ungeplante Stillstände, lange Fehlerdiagnosen und Personalengpässe bei der Wartung schnell zu erheblichen Produktivitätsverlusten. Hinzu kommen heterogene Maschinenparks, wachsende Komplexität durch Digitalisierung sowie der Wunsch nach maximaler Anlagenverfügbarkeit – bei zugleich begrenzten personellen und finanziellen Ressourcen.
Spezifische Anforderungen der Zielgruppe
Technische Leiter und Produktionsleiter benötigen Lösungen, die sowohl technisch belastbar als auch wirtschaftlich überzeugend sind. Sie suchen nach Ansätzen, die sich nahtlos in bestehende Prozesse integrieren lassen, Wartung planbar machen und ein Höchstmaß an Transparenz über den Anlagenzustand bieten – ohne zusätzliche IT- oder Personalaufwände. Im Fokus steht die Forderung: „Verfügbarkeit sichern, Ausfälle minimieren, Kosten dauerhaft senken.“
Genau an dieser Schnittstelle setzt Greif-Velox mit der Entwicklung intelligenter Wartungslösungen wie VeloGuard an. Als Enabler für Predictive Maintenance verbindet VeloGuard automatisierte, datenbasierte Zustandsüberwachung mit nutzerfreundlicher Integration ins Bedienkonzept der Anlage. So wird Predictive Maintenance im Alltag der Produktion nicht nur technisch möglich, sondern vor allem wirtschaftlich sinnvoll und praxisnah umsetzbar.
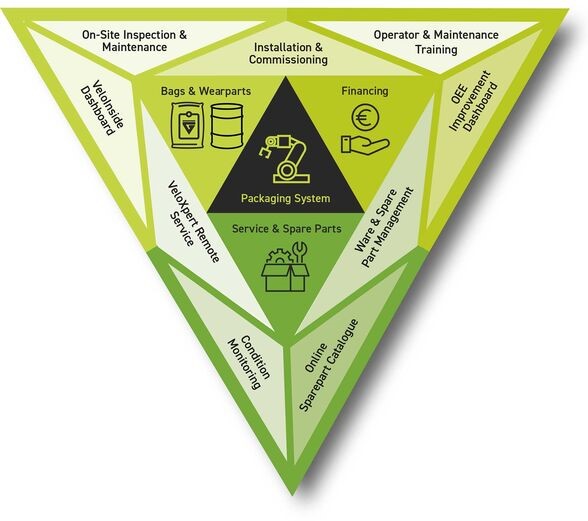
VeloGuard: Praxisbeispiel für intelligente, vorausschauende Wartung
VeloGuard ist ein Condition-Monitoring-System, das zentrale pneumatische Komponenten einer Greif-Velox-Anlage fortlaufend überwacht. Mittels automatisierter Selbsttest-Funktion werden relevante Bauteile – wie Produkteinlaufklappen oder Entlüftungsfunktionen – zyklisch geprüft und deren Zustand direkt auf dem HMI (Human Machine Interface) der Maschine visualisiert. Potenzielle Fehler und Verschleißerscheinungen werden im Klartext angezeigt; so kann das Bedienpersonal umgehend reagieren.
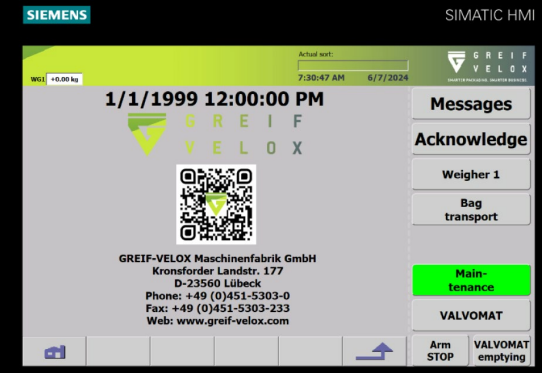
Überwachte Komponenten und Diagnosestrategien
Besonders im Fokus stehen Komponenten, deren Ausfall kritische Folgen für die Prozesssicherheit oder Produktqualität hätte. VeloGuard erkennt zum Beispiel frühzeitig Undichtigkeiten an Produkteinlaufklappen oder Funktionsstörungen an Kesselentlüftungen. Durch die intelligente Kombination von Echtzeitdaten, Klartextdiagnose und automatisierten Prüfzyklen können bereits kleinste Abweichungen erfasst und frühzeitig kommuniziert werden. Die Integration in das bestehende HMI ermöglicht dabei eine sofortige Handlungsanweisung für das Bedienpersonal.
Die MMW Mineralmahlwerk Hamm GmbH hat die VeloGuard Selbsttest-Funktion in ihre Produktion integriert – mit eindrucksvollem Ergebnis: Die Ausfallzeiten der relevanten Anlage konnten um 90 % gesenkt, der Personalaufwand für Wartung um 80 % reduziert werden. Gleichzeitig stieg die Anlagenproduktivität signifikant. Diese Ergebnisse belegen, dass Predictive Maintenance in Verbindung mit Greif-Velox-Technologie einen direkten wirtschaftlichen Mehrwert schafft und ungeplante Stillstände nahezu eliminiert werden können.
Einbindung in bestehende Wartungs- und Instandhaltungsprozesse
VeloGuard lässt sich unkompliziert in bestehende Instandhaltungsstrukturen integrieren. Die Nachrüstung erfordert lediglich einen Umbausatz, eine Software-Erweiterung und Anpassungen an Bediengerät und E-Plan. Die Zustandsüberwachung erfolgt automatisiert, der Wartungsbedarf wird vorausschauend gemeldet – Wartungsfenster können gezielt geplant und Ressourceneinsatz optimiert werden. Die Verantwortung bleibt beim Kunden; komplexe Serviceeinsätze und unnötige Stillstände werden jedoch minimiert.
Wirtschaftliche Bewertung und ROI
Die Einführung von Predictive Maintenance mit Systemen wie VeloGuard ist wirtschaftlich klar messbar. Bereits mit der Reduktion ungeplanter Stillstände ergeben sich signifikante Einsparungen, die sich oft innerhalb kurzer Zeit amortisieren. Das Beispiel der MMW Mineralmahlwerk Hamm GmbH zeigt: Nach Implementierung der VeloGuard-Selbsttest-Funktion sanken die Ausfallzeiten um 90 % und der Personalaufwand für Wartung um 80 %. Dadurch wurden nicht nur Reparaturkosten reduziert, sondern auch teure Produktionsausfälle vermieden und die Gesamtanlageneffektivität (OEE) deutlich gesteigert.
Typische KPI zur Bewertung des wirtschaftlichen Nutzens von Predictive Maintenance:
- OEE (Overall Equipment Effectiveness): Zeigt die tatsächliche Produktivität der Anlage im Verhältnis zum theoretischen Maximum. Eine OEE-Steigerung von wenigen Prozentpunkten hat oft massive Effekte auf den Output und damit den Unternehmenserfolg.
- MTBF (Mean Time Between Failures): Die mittlere Zeit zwischen zwei Ausfällen ist ein direkter Indikator für die Verfügbarkeit der Anlage.
- Instandhaltungskosten: Durch gezielte, zustandsorientierte Wartung sinken sowohl direkte Wartungskosten als auch die Kosten für Folgeschäden und ungeplante Serviceeinsätze.
Technische Umsetzung und Integration
Die Integration von Predictive-Maintenance-Lösungen wie VeloGuard in bestehende Produktionssysteme ist gezielt auf eine einfache Nachrüstbarkeit ausgelegt:
Schritte zur Einführung:
- Analyse: Identifikation der kritischen Komponenten und Prozesse, die für das Condition Monitoring überwacht werden sollen
- Umrüstsatz: Einbau von Sensorik, Nachrüstung der Hardware und Integration ins Steuerungskonzept der Anlage
- Softwareintegration: Installation und Parametrierung der Diagnose-Software sowie Anbindung an die bestehenden Visualisierungen (z. B. HMI)
- HMI-Anpassung: Integration der Zustandsanzeigen, Klartextmeldungen und Wartungsempfehlungen direkt ins Bediengerät der Maschine
Anforderungen an IT-/Datensicherheit
Die Übertragung und Verarbeitung sensibler Maschinendaten erfolgt bei Greif-Velox stets mit höchsten IT-Sicherheitsstandards. Eine Anbindung an das Unternehmensnetzwerk ist nicht erforderlich; der Remote-Zugriff erfolgt über eine gesicherte Verbindung, die nur bei Bedarf durch einen Schalter aktiviert werden kann. So bleibt die Datensouveränität beim Betreiber, und Risiken durch Cyber-Angriffe werden minimiert.
Schnittstellen zu bestehenden Produktionssystemen
VeloGuard ist so konzipiert, dass eine Integration in bestehende Automatisierungs- und Wartungsprozesse ohne tiefgreifende Systemänderungen möglich ist. Die Lösung arbeitet systemoffen und lässt sich in bestehende Dashboards, Wartungsmanagement-Software oder ERP-Systeme einbinden, um den Informationsfluss zwischen Produktion, Instandhaltung und Management zu optimieren.
Zukunftsausblick: Predictive Maintenance als Baustein der Smart Factory
Predictive Maintenance markiert den Wandel hin zur Smart Factory. Mit fortschreitender Digitalisierung, dem Einsatz von Künstlicher Intelligenz und der durchgängigen Vernetzung von Anlagen wächst das Potenzial, Wartung nicht nur vorausschauend, sondern zunehmend autonom und selbstoptimierend zu gestalten. KI-basierte Analyseverfahren erkennen Muster im Anlagenbetrieb, prognostizieren den optimalen Wartungszeitpunkt und ermöglichen so einen reibungslosen, nahezu ausfallfreien Produktionsprozess.
In diesem Kontext positioniert sich Greif-Velox als Innovationspartner für den Mittelstand und die Industrie. Mit Lösungen wie VeloGuard, die Predictive Maintenance praxistauglich und wirtschaftlich integrieren, leistet Greif-Velox einen aktiven Beitrag zur nachhaltigen Produktionsoptimierung. Die konsequente Weiterentwicklung intelligenter, vernetzter Systeme schafft die Grundlage, um zukünftige Herausforderungen der Industrie 4.0 erfolgreich zu meistern – von der Ressourcenoptimierung über den flexiblen Personaleinsatz bis hin zur maximalen Prozesssicherheit und -transparenz.
Wer heute auf Predictive Maintenance mit Greif-Velox setzt, schafft die Basis für eine effiziente, zukunftsfähige Produktion – und damit einen nachhaltigen Wettbewerbsvorteil im Zeitalter der Digitalisierung.