Predictive Maintenance: production optimization through preventive system maintenance
Production downtime is one of the most expensive and at the same time most avoidable risks in the industrial environment. Unplanned downtimes not only lead to direct losses in sales, but also affect on-time delivery, customer relationships and ultimately the competitiveness of the entire company. Internal analyses and independent studies show that even short downtimes cause enormous costs - especially when processes are highly automated and act as a bottleneck in the value stream.
Traditional maintenance and servicing concepts, such as purely reactive or time-based maintenance, are reaching their limits in the face of increasing system complexity and digitalization. Unpredictable faults, time-consuming troubleshooting and long service response times often result in six-figure costs per year and system. At the same time, there is growing pressure to continuously increase plant availability, product quality and resource efficiency - without additional costs for personnel and budget.
In this area of conflict, Predictive Maintenance is establishing itself as a central lever for a future-oriented maintenance strategy. Through intelligent monitoring, data-based analysis and automated early warning systems, potential failures can not only be detected at an early stage, but also specifically avoided. Predictive maintenance thus creates the prerequisites for optimally planning maintenance windows, drastically reducing unplanned downtimes and significantly extending the service life of machines.
Greif-Velox addresses these challenges with innovative, tried-and-tested solutions. With digital tools such as VeloGuard, Greif-Velox integrates predictive maintenance principles directly into its own plant environment - and thus creates measurable added value for production companies that strive for maximum plant availability, maximum process reliability and predictable maintenance. You can find out how this approach works in practice and what advantages predictive maintenance offers in conjunction with Greif-Velox systems in the rest of this article.
What is Predictive Maintenance?
Predictive Maintenance describes a maintenance strategy in which failures and wear are no longer treated reactively or at fixed intervals, but are detected and prevented in advance through continuous monitoring and data-based analysis. The aim is to evaluate the actual use and current condition of the machine in real time in order to accurately predict the optimum maintenance time.
Differentiation from classic maintenance concepts:
Compared to reactive maintenance, where action is only taken in the event of a malfunction, and preventive maintenance, which is based on fixed maintenance intervals, predictive maintenance enables a maximum degree of planning reliability and resource efficiency. While reactive approaches can lead to unplanned downtime and consequential damage, preventive methods often result in unnecessary maintenance work and the associated costs. Predictive Maintenance combines the best of both worlds: Maintenance takes place when it is actually necessary and makes economic sense.
Core elements: condition monitoring, data analysis, AI
At the heart of Predictive Maintenance is Condition Monitoring - i.e. the permanent condition monitoring of relevant components and processes. Sensors record operating parameters such as temperature, pressure, vibration, running times or switching cycles in real time. The resulting data is evaluated using modern analysis methods in order to identify trends and deviations at an early stage.
Modern Predictive Maintenance systems use advanced algorithms and, increasingly, artificial intelligence (AI) to identify complex correlations between process parameters and potential causes of failure. This results in digital early warning systems that enable a precise forecast of the remaining useful life (RUL) of components or systems and automatically report maintenance requirements.
Technical requirements for Predictive Maintenance
Various technical requirements must be met in order to implement Predictive Maintenance:
- Sensors and automation: The system must be equipped with suitable sensors for monitoring all relevant components.
- Data infrastructure: Secure, fast recording, storage and transmission of sensor data - often in real time - is the basis for any analysis.
- Analysis and evaluation software: Algorithms, AI tools or special software solutions automatically evaluate the data and derive recommendations for action.
- Integration into the operating and maintenance system: Ideally, the status data and maintenance recommendations are integrated directly into the HMI (Human Machine Interface) and the existing maintenance organization so that those responsible always have an overview.
This infrastructure not only allows machines and systems to be operated more efficiently, but also virtually eliminates unplanned downtime. Greif-Velox uses these principles consistently in its own product world - including with the VeloGuard condition monitoring system.
Historical development from “Breakdown Maintenance” to “Predictive Maintenance”
Maintenance in industrial production has undergone a fundamental change in recent decades. Originally, purely reactive approaches dominated: Machines and systems were only serviced once a defect or failure had already occurred (breakdown maintenance). This strategy often led to long downtimes, unplannable costs and reduced output.
With increasing automation and rising cost pressure, preventive maintenance was established. Maintenance was carried out at fixed intervals, regardless of the actual condition of the machine. Although this prevented many breakdowns, it quickly became clear that unnecessary maintenance work and the replacement of components that were still intact led to inefficient use of resources and avoidable costs.
The logical further development of this approach is condition-based and predictive maintenance. Modern sensor technology, digitalization and intelligent data analysis are used to permanently monitor the current condition of all critical components. Predictive Maintenance makes it possible to precisely predict maintenance requirements and optimally plan maintenance measures - thus reducing unplanned downtime and costs in the long term.
Importance of Total Productive Maintenance (TPM) as a strategic basis
Total Productive Maintenance (TPM) is regarded as a pioneering philosophy for efficient and sustainable maintenance in the industrial environment. TPM combines operational excellence with company-wide involvement - from plant management to plant operators. The aim is to eliminate all sources of loss, maximize plant availability and systematically increase productivity through continuous improvement.
The eight TPM pillars - from autonomous maintenance (Jishu Hozen) to focused improvements (Kaizen), planned maintenance, quality, training and safety management through to development-accompanying maintenance - provide the organizational framework on which modern predictive maintenance concepts are also based. Only the combination of TPM principles with data-based predictive maintenance unlocks the full potential of digital maintenance strategies.
Changing success factors: from reactive to proactive maintenance
The shift from reactive to proactive maintenance is characterized by technological progress and a changed understanding of roles in production. While maintenance was seen as a “necessary evil” in traditional structures, the focus of value creation is now shifting to plant availability, resource efficiency and process reliability. Predictive Maintenance builds on the lessons of TPM and uses modern technologies to make the goal of loss-free production tangible.
Companies that implement this paradigm shift at an early stage and combine their maintenance strategy with TPM and Predictive Maintenance principles will secure sustainable competitive advantages - through higher plant availability, reduced maintenance costs and a measurable increase in productivity.
Economic effects: Less downtime, lower costs, higher OEE
Predictive Maintenance unfolds its economic benefits in particular through the drastic reduction of unplanned downtimes. The better failures are predicted and avoided, the higher the plant availability - a key driver for productivity (Overall Equipment Effectiveness, OEE) and for the company's competitiveness.
Up to 90% of downtimes can be avoided thanks to continuous monitoring and automatic diagnostics. Practical examples - such as the Hamm mineral grinding plant, which uses the VeloGuard self-test function from Greif-Velox - prove this: Maintenance costs have been reduced by up to 80% and unplanned production downtime has been almost completely eliminated.
Increased machine availability and extended service life
Predictive Maintenance detects wear at an early stage and carries out targeted maintenance, keeping machines in optimum operating condition at all times. This not only leads to consistently high system availability, but also significantly extends the service life of critical components and the entire system. Expensive emergency repairs and consequential damage caused by secondary defects are prevented and maintenance budgets can be managed more efficiently.
Improved planning of maintenance windows
Another decisive advantage is the ability to plan maintenance measures with foresight and in line with production schedules. Planned maintenance windows can be optimally integrated into production cycles, allowing necessary interventions to be postponed to non-productive times or scheduled downtimes. This reduces the number of unplanned breakdowns and expensive ad-hoc interventions to a minimum. Companies gain full control over their maintenance processes and increase their delivery reliability.
Increasing occupational safety
Predictive Maintenance makes a significant contribution to occupational safety: Regular, condition-based inspections and the timely replacement of safety-relevant components minimize the risk of accidents and dangerous operating conditions. In addition, automated fault detection enables even less experienced employees to recognize maintenance requirements at an early stage and act correctly - safety in the production environment is raised to a new level.
Challenges of typical production companies
Production companies in the SME sector are under high pressure to be efficient. Unplanned downtimes, lengthy fault diagnoses and staff shortages during maintenance can quickly lead to significant productivity losses, especially with automated systems. Added to this are heterogeneous machinery, growing complexity due to digitalization and the desire for maximum plant availability - with limited human and financial resources.
Specific requirements of the target group
Technical managers and production managers need solutions that are both technically resilient and economically convincing. They are looking for approaches that can be seamlessly integrated into existing processes, make maintenance plannable and offer maximum transparency regarding the system status - without additional IT or personnel costs. The focus is on the requirement: “Ensure availability, minimize downtime, permanently reduce costs.”
This is precisely where Greif-Velox comes in with the development of intelligent maintenance solutions such as VeloGuard. As an enabler for predictive maintenance, VeloGuard combines automated, data-based condition monitoring with user-friendly integration into the system's operating concept. This makes predictive maintenance not only technically possible in everyday production, but above all economically viable and practical to implement.
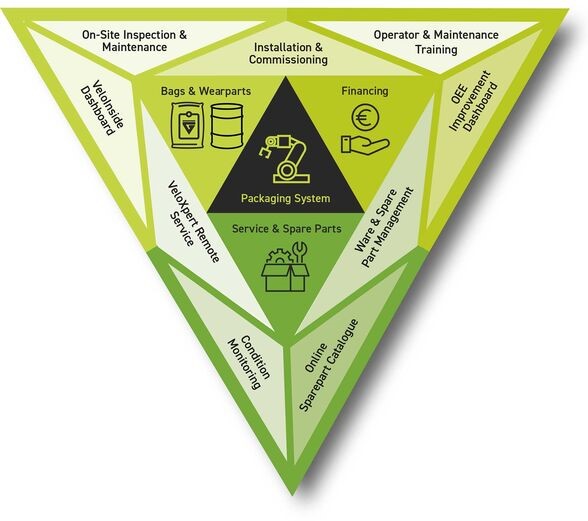
VeloGuard: practical example of intelligent, predictive maintenance
VeloGuard is a condition monitoring system that continuously monitors the central pneumatic components of a Greif-Velox system. Using an automated self-test function, relevant components - such as product infeed flaps or venting functions - are checked cyclically and their condition is visualized directly on the machine's HMI (Human Machine Interface). Potential faults and signs of wear are displayed in plain text, allowing the operating personnel to react immediately.
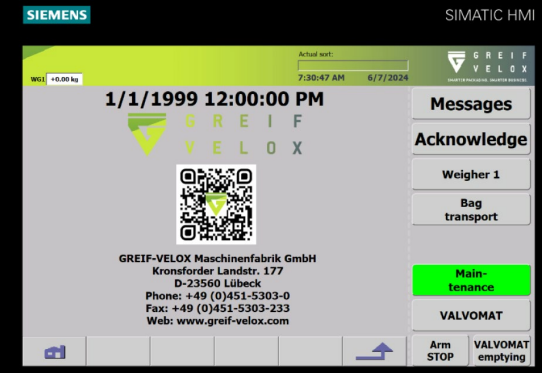
Monitored components and diagnostic strategies
The focus is particularly on components whose failure would have critical consequences for process reliability or product quality. For example, VeloGuard detects leaks in product inlet flaps or malfunctions in boiler vents at an early stage. Thanks to the intelligent combination of real-time data, plain text diagnostics and automated test cycles, even the smallest deviations can be detected and communicated at an early stage. Integration into the existing HMI enables immediate instructions for the operating personnel.
MMW Mineralmahlwerk Hamm GmbH has integrated the VeloGuard self-test function into its production - with impressive results: downtimes of the relevant plant have been reduced by 90% and personnel costs for maintenance have been cut by 80%. At the same time, plant productivity increased significantly. These results prove that predictive maintenance in conjunction with Greif Velox technology creates direct economic added value and unplanned downtimes can be virtually eliminated.
Integration into existing maintenance and servicing processes
VeloGuard can be easily integrated into existing maintenance structures. Retrofitting only requires a conversion kit, a software extension and adjustments to the control unit and E-plan. Condition monitoring is automated, maintenance requirements are reported in advance - maintenance windows can be planned specifically and the use of resources optimized. Responsibility remains with the customer; however, complex service calls and unnecessary downtimes are minimized.
Economic evaluation and ROI
The introduction of Predictive Maintenance with systems such as VeloGuard is clearly measurable in economic terms. The reduction in unplanned downtime alone results in significant savings that often pay for themselves within a short period of time. The example of MMW Mineralmahlwerk Hamm GmbH shows this: After implementing the VeloGuard self-test function, downtimes fell by 90% and personnel costs for maintenance by 80%. This not only reduced repair costs, but also avoided expensive production downtime and significantly increased overall equipment effectiveness (OEE).
Typical KPIs for evaluating the economic benefits of predictive maintenance:
- OEE (Overall Equipment Effectiveness): Shows the actual productivity of the plant in relation to the theoretical maximum. An OEE increase of just a few percentage points often has a massive impact on output and therefore the company's success.
- MTBF (Mean Time Between Failures): The mean time between two failures is a direct indicator of the availability of the system.
- Maintenance costs: Targeted, condition-based maintenance reduces both direct maintenance costs and the costs of consequential damage and unplanned service calls.
Technical implementation and integration
The integration of Predictive Maintenance solutions such as VeloGuard into existing production systems is specifically designed for easy retrofitting:
Steps for implementation:
- Analysis: Identification of the critical components and processes to be monitored for condition monitoring
- Conversion kit: Installation of sensors, retrofitting of the hardware and integration into the control concept of the system
- Software integration: Installation and parameterization of the diagnostic software and connection to the existing visualizations (e.g. HMI)
- HMI adaptation: Integration of status displays, plain text messages and maintenance recommendations directly into the machine's operating device
IT/data security requirements
At Greif-Velox, sensitive machine data is always transmitted and processed in accordance with the highest IT security standards. A connection to the company network is not required; remote access takes place via a secure connection that can only be activated by a switch if necessary. This means that data sovereignty remains with the operator and risks from cyber attacks are minimized.
Interfaces to existing production systems
VeloGuard is designed in such a way that it can be integrated into existing automation and maintenance processes without extensive system changes. The solution is system-open and can be integrated into existing dashboards, maintenance management software or ERP systems to optimize the flow of information between production, maintenance and management.
Outlook for the future: Predictive maintenance as a building block of the smart factory
Predictive Maintenance marks the shift towards the smart factory. With advancing digitalization, the use of artificial intelligence and the end-to-end networking of systems, there is growing potential to make maintenance not only predictive, but increasingly autonomous and self-optimizing. AI-based analysis processes recognize patterns in plant operation, predict the optimal maintenance time and thus enable a smooth, virtually failure-free production process.
In this context, Greif-Velox is positioning itself as an innovation partner for SMEs and industry. With solutions such as VeloGuard, which integrate predictive maintenance in a practical and economical way, Greif-Velox makes an active contribution to sustainable production optimization. The consistent further development of intelligent, networked systems creates the basis for successfully mastering the future challenges of Industry 4.0 - from resource optimization and flexible personnel deployment to maximum process reliability and transparency.
Those who rely on Predictive Maintenance with Greif-Velox today create the basis for efficient, future-proof production - and thus a sustainable competitive advantage in the age of digitalization.