Customers in
92 countries
> 92 % customer loyalty
for follow-up projects
Certified according to
ISO 9001 & 14001
24-hour service
365 days a year
The VeloXpert program: our 360° service promise
With VeloXpert, we offer you more than just service - we offer a partnership. This programme covers all points of contact in the life cycle of your system, from commissioning and predictive maintenance to continuous optimization. All our services are designed to safeguard your production, increase efficiency (OEE) and guarantee you maximum predictability.
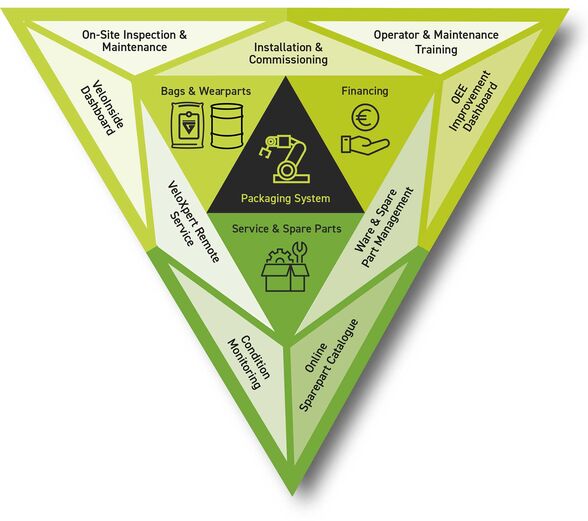
At your side for the life of the system
-
Concept & Design
Service expertise flows into the planning right from the start.
-
Factory Acceptance Test (FAT)
We ensure that your system meets the requirements at our factory. This guarantees smooth commissioning at your site.
-
Setup & commissioning
Our specialists install the system at your site and ensure a perfect production start (Site Acceptance Test, SAT).
-
Operation & Optimization
We support you with service level agreements (SLAs), 24-hour remote service and proactive readjustments to improve performance.
-
Service & maintenance
Regular inspections and the replacement of OEM wear parts ensure longevity and performance.
-
Electronic spare parts catalog
Simple search and fast ordering of the right spare parts.
-
Predictive Maintenance
With systems such as VeloGuard, we monitor critical components automatically: a service before the fault that prevents failures before they even occur.
-
Repair & troubleshooting
Our helpdesk solves up to 95% of all faults remotely. If necessary, our technicians will be with you as quickly as possible.
-
Modernization & Retrofit
We make your system fit for the future by replacing outdated components and integrating new technologies.
Our service modules for your success
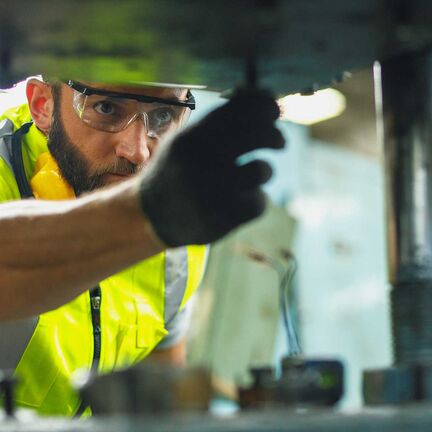
System modernization & retrofit
Secure your production, even if manufacturers discontinue components such as the Siemens OP control system or Bizerba ST weighing technology. We equip your system with the latest technology and ensure the supply of spare parts for over ten years.
Increased operational safety
Continuous availability of spare parts
Integration into modern ERP systems
Predictive maintenance with VeloGuard
Avoid unplanned downtimes with automatic wear monitoring. Our VeloGuard system automatically checks compressed air-operated shut-off devices and reports the need for replacement directly on the system's HMI.
No more time-consuming trouble
Reliable production times
Downtimes can be planned

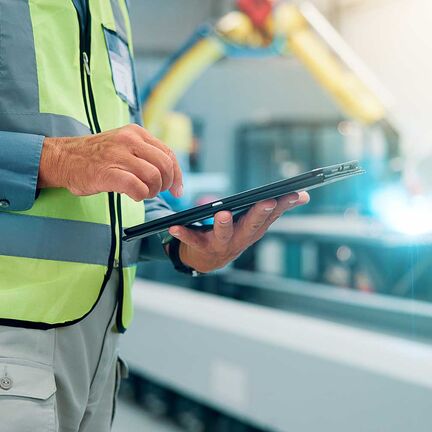
Electronic spare parts catalog
Find original spare and wear parts quickly and accurately in our digital catalog. Individually tailored to your system.
Express delivery service
High-quality OEM parts
Minimization of production downtimes
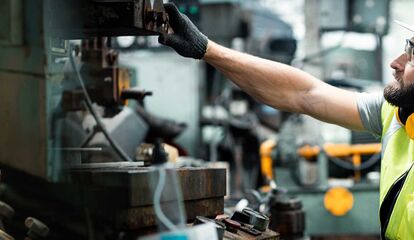
Service & maintenance
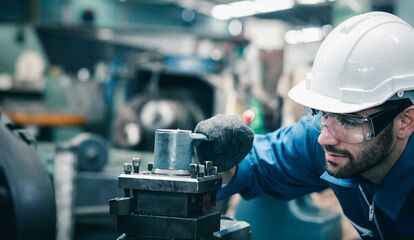
Troubleshooting & 24h support
The perfect start to a long partnership
A successful Factory Acceptance Test (FAT) is the foundation for maximum system availability. Here you can see how we create the basis for long-term efficient production for our customers in the chemical and food industries.
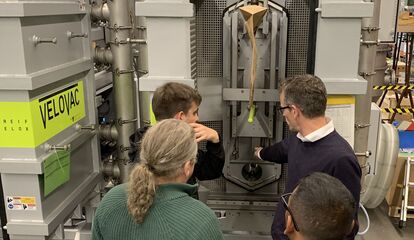
Dust-free production in the specialty chemicals industry
Customer: Cabot BV (Botlek)
System: Full-line solution with VeloVac vacuum packer
Project: Realization of a dust-free bagging system for ultra-light powders such as carbon black, accepted in a successful FAT
Service aspect: The clean, dust-free VeloVac technology not only ensures product quality, but also significantly minimizes ongoing cleaning and maintenance work.
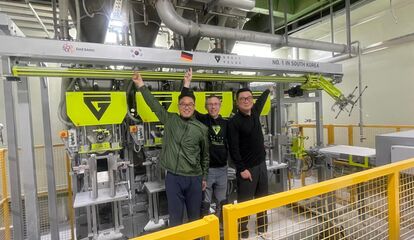
Maximum performance and safety for food
Customer: Daesang Corporation
System: Quadruple version of the BVPV gross pneumatic packer
Project: Installation of a high-performance line (600 bags/h) with food-grade components and integrated combination checker for quality control
Service aspect: Integrated weighing and metal ejection guarantee maximum product safety, the function of which is permanently ensured by our regular service checks and calibrations.
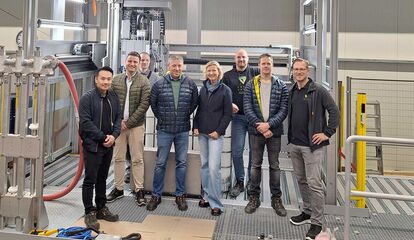
Fully automatic and ATEX safety
Customer: Allnex
System: Two fully automatic filling systems of the type A-DOS-P1
Project: Commissioning of a full-line solution with robot labeling and load securing for use in ATEX zones
Service aspect: ATEX certification guarantees maximum occupational safety. Our service team provides support with the regular, legally required inspections in order to maintain this standard over the entire service life of the system.
The next level of service: Packaging as a Service (PaaS)
Convert high initial investments (CAPEX) into predictable monthly operating costs (OPEX)
For bagging ultra-light powders, we go one step further with our PaaS model. Instead of buying a machine, you get a complete end-to-end solution at a fixed monthly price. We bundle machine provision, financing, maintenance, spare parts and even the appropriate consumables such as high-performance bags from dy-pack. This allows you to concentrate fully on your core business while we manage your packaging processes.
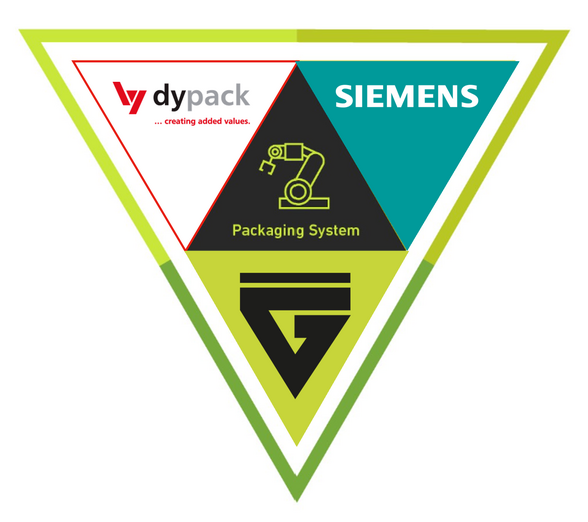
Full cost control:
A fixed monthly price for maximum predictability
No capital commitment:
Avoid high initial investments and protect your budget
All-round carefree package:
We take care of installation, maintenance and the supply of spare and consumable parts
Flexible packages:
Choose the model that suits you:
Total Care: Financing, service, bags and all parts
Essential Care: Service, bags and parts without financing
Individual Care: A freely selectable combination of services
Click here to go directly to your service and spare parts contact
Direct contact to GREIF-VELOX: Here you will find your contact person.
Find your contact person