Suitable filling processes for canister filling
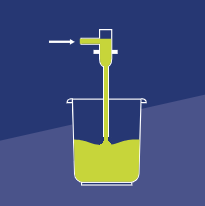
Below bunghole filling
Specially developed for closed containers where the liquid is supplied through a bunghole. This variant is suitable for non-foaming and uncomplicated liquids and ensures precise filling.
Above level filling
Suitable for uncomplicated, non-foaming products. With this method, the liquid comes out of the dosing element above the liquid level, ideal for open and closed (bunghole) containers.
Below level filling
This method is suitable for foaming products or if explosive gases can be released during filling. The liquid exits below the liquid surface, which prevents foam and electrostatic charges in flammable materials.
GREIF-VELOX solutions from
practice for canister filling
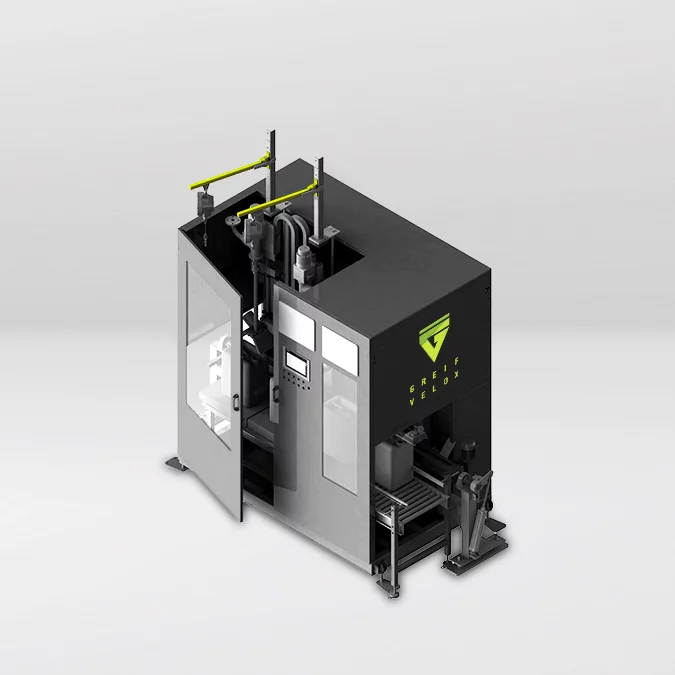
A-DOS-K
A fully automatic filling system for up to 450 canisters per hour. The system offers automatic container separation, automatic canister transport, automatic filling with one to three filling valves and automatic canister closing.
Advantages
Canister filling in a class of its own: automatic valve changes, an output of up to 450 canisters per hour, bidirectional ERP connection and a closed housing for optimal accessibility.
High productivity: Optimizes daily processes and ensures smooth canister filling at the highest level.
Versatility: Suitable for production managers and technical managers in industries such as chemical, petrochemical and food industries.
Seamless integration: into existing manufacturing processes and maximum efficiency when filling canisters.
Options
Safety devices: Use of additional options such as inerting, overfill shut-off or collecting trays to increase safety.
Higher automation: Through the modular system with options such as controlled valve upward movement or motorized valve base height adjustment.
Cleaning and hygiene: Good cleaning ability of the parts in contact with the product and availability of special cleaning equipment.
Material selection: Available in stainless steel and special materials for parts in contact with the product.
Adaptation and integration: Opportunities for interaction with the customer's product feed and integration into customer's control systems in order to best integrate the system into existing production environments.

Save money with standard solutions.
Earn money with individual solutions.
Our philosophy at Greif-Velox is to offer individually tailored solutions instead of standard products.
Each liquid filling system is tailored precisely to the needs and processes of our customers to enable rapid integration into existing product lines or the development of a completely coordinated full-line system.
We attach great importance to precision, safety and automation in order to increase our customers' production efficiency with maximum flexibility.
MAXIMUM EFFICIENCY AND FLEXIBILITY THROUGH FULL-LINE SYSTEMS
Specific filling requirements necessitate individual system solutions
Greif-Velox liquid filling systems are specifically designed to meet the diverse requirements of industries such as chemicals, food and petrochemicals.
Custom-made products for special needs
Temperature-sensitive liquids: Realization of heated filling systems GMP-compliant solutions: Developed specifically for the food and pharmaceutical sectors Personnel savings: Processes optimized through automation.
Precision in every drop
Product-specific valves: ensure accurate dosing Adaptation to container types: flexibility for canisters, drums and IBCs Automatic opening and closing: ensures the integrity of the end product.
Purity and security
Clean production environments through integrated solutions Increased efficiency and safety through systems made of stainless steel or plastic.
Holistic system solutions through full-line filling systems
As part of a closed production system, our filling systems for liquids go far beyond the pure filling function: they form an integral part of an overall system that fits seamlessly into existing production lines and complements them.
Our full-line systems are able to serve complex requirements from container preparation and filling to post-processing and storage, which makes us a holistic system provider in production technology.
The focus is on individual adaptation in order to ensure optimal integration into the respective operational processes.
Find the right contact person
Direct contact to GREIF-VELOX or competent trading partner at your location:
You will find the right contact person for your request here.