The customer

The GoodMillsGroup, Europe's largest milling company, operates eight locations through its subsidiary GoodMills Deutschland where quality and specialty flours, legumes and rice are produced. At the Hildebrandmühle in Mannheim, GoodMills Germany focuses on the production, bagging and packaging of various durum wheat products. With an annual capacity of more than 180,000 tons, the Hildebrandmühle is one of the largest durum mills in Germany.
The starting point
At the Mannheim location, GoodMills Germany planned to expand the already diverse production with two additional production lines. However, the previous system could no longer withstand current technological developments and an increase in bagging capacity was necessary. For this reason, the company decided to invest in a new, more flexible system. This should not only correspond to the latest state of the art, but also be expandable and optimized in the future in order to meet future challenges
The request
For the expansion in Mannheim, GoodMills Germany needed a system that was able to process fine flour (with a grain size of less than 200 micrometers), fine-grained semolina (200 to 800 micrometers) and meals (2 to a maximum 4 millimeters) can be filled flexibly and precisely into bags between five and 25 kilograms
The new filling system should offer the possibility of carrying out product changes quickly and with minimal cleaning effort. A key goal was to double the output compared to the old system and achieve around 400 bags per hour.
In addition, the system should be expandable if necessary in order to increase the capacity to up to 600 bags per hour without having to carry out extensive renovation work. It was also necessary that the system components could be easily integrated into existing command and control systems. The choice fell on the GREIF-VELOX BVPV 4.40 Full-Line, which meets these specific needs.
The solution
GoodMills Germany chose the GREIF-VELOX gross pneumatic packer BVPV 4.40, which uses innovative technology to ensure the highest possible efficiency in the bagging process of semolina, flour and meals. This decision led to a significant optimization of the production processes.
The features
- Smooth processes and reduced personnel costs:
Use of the GREIF-VELOX Valvomat, which automatically opens the empty bag and positions it correctly on the filler neck - Tear-resistant welding:
The ultra-sealing unit ValvoSeal with patented waffle technology ensures that the bags are securely closed after filling - Lower complaint costs:
The space-saving combination checker combines a metal detector with an integrated checkweigher that works with a detection accuracy of less than two millimeters - Automatic, precise and time-saving palletizing:
using the four-axis palletizing robot VeloPack - Automatic transport:
The filled bags are guided via roller conveyors to a wrapper for securing the load - Quick and easy product changes:
possible thanks to mechanical features such as the motorized sack chair height adjustment - Continuous process optimization:
through the “transparent packer”, which records, evaluates and manages process data, which makes the filling of various products easier - Significantly reduced cleaning effort and times:
thanks to the pneumatically folding residual emptying base and a special residual emptying function
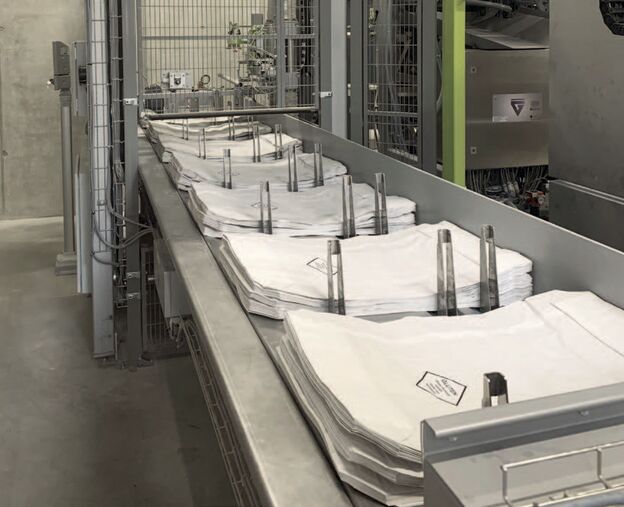
The result: resounding success at GoodMills Germany
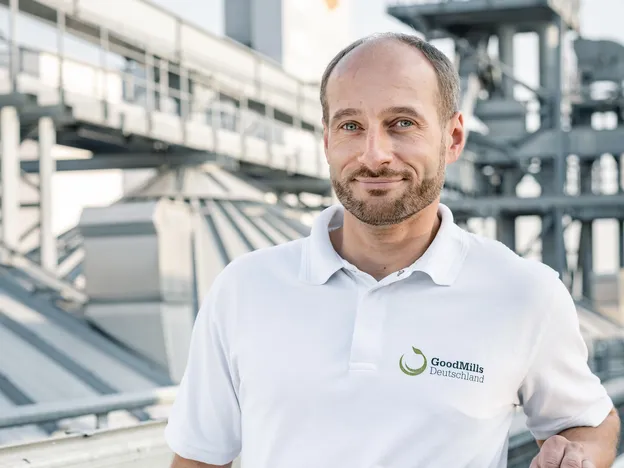
With the implementation of the new GREIF-VELOX system, GoodMills Germany has already doubled its production output. In addition, the detailed documentation of the process parameters offers the opportunity to further increase efficiency in the future. “The process data allows us to coordinate the processes even better,” explains Alexander Wieler, plant manager at GoodMills. He emphasizes that the seamless communication between the machine components was a decisive factor in choosing GREIF-VELOX: “The programming from a single company ensures clear interfaces, in contrast to our experiences with competitors.”
Another advantage of the new system is the high level of automation, which made it possible to save one staff position. Optimizations such as the improved boiler outlet significantly reduce downtime during product changes, which further increases productivity. “The systems are designed to run very well when empty, which significantly reduces cleaning times,” adds Wieler. Product changes are simplified by quickly selecting saved filling parameters and bag formats at the push of a button.
In addition, a further increase in efficiency was achieved through the use of a space-saving and faster palletizing robot. Wieler, who was initially skeptical as to whether the robot could deliver a pallet image as clean as a layer palletizer, confirms: “But this one also works to the fullest satisfaction.”
GoodMills Germany also benefits from the time-saving remote service from GREIF-VELOX, which offers quick support with commissioning, configuring the system and other questions. This ensures that a contact person is available at all times to ensure optimal support.