Case studies for increasing efficiency and flexibility with GREIF-VELOX systems
Through innovative engineering solutions for more precise, faster and safer systems
We demonstrate how GREIF-VELOX uses individually tailored filling systems and packaging systems to improve production speed, measurement accuracy and operational safety in specific production facilities worldwide. Our detailed case studies illustrate diverse success stories in the chemical, food and other sectors, supported by quantitative results and real improvements.
Chemical and food industry
Innovative solids filling system for ICL Ladenburg
The solid filling system from GREIF-VELOX at ICL Ladenburg led to a significant reduction in complaint and cleaning costs, which were originally caused by incorrectly welded bags. This cost problem, which amounted to at least 20,000 euros annually, was radically improved by the introduction of the ValvoDetect on the BVP air packer. With its optical sensors, ValvoDetect ensures that only correctly positioned bags are welded by detecting and sorting out incorrectly attached bags before welding.
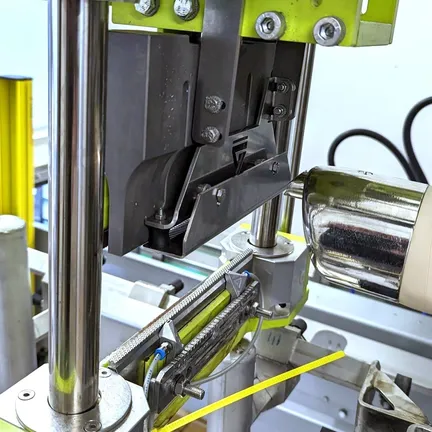
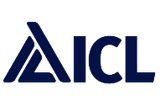
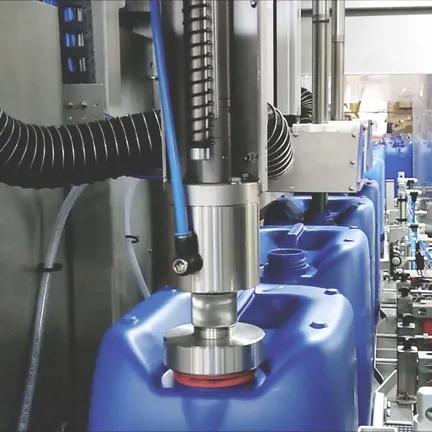
Chemical industry
Hydrogen peroxide filling system for Evonik
Our filling system at the chemical company Evonik led to an impressive increase in filling speed by 50 percent. Additionally, we significantly improved product safety by implementing advanced contamination control measures integrated into a highly automated hydrogen peroxide filling system, increasing not only efficiency but also workplace safety.
Food industry
Bagging system for GoodMills Germany
At the food producer GoodMills Germany, we were able to significantly increase packaging efficiency by 100 percent thanks to our systems. We also maximized the accuracy of the filling processes, doubling production output to up to 400 bags per hour, while at the same time minimizing cleaning effort and changeover times by using our gross pneumatic packer BVPV 4.40.
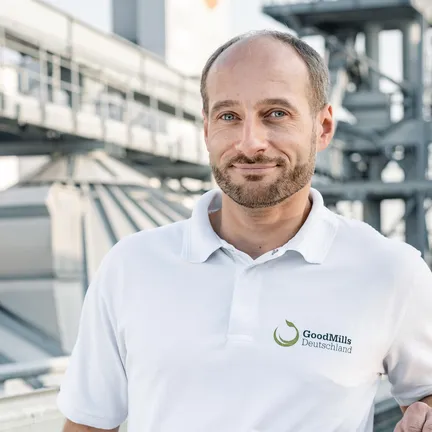
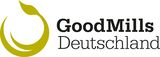
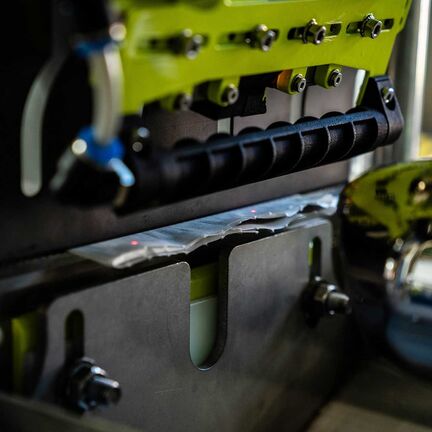
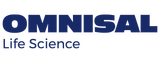
Food industry
Bagging system for Omnisal
The new full-line bagging system with the Greif-Velox BVPV 4.40 high-speed air packer optimises the bagging of phosphate mixtures at Omnisal. With a hygienic design made of stainless steel, a fully automated complete bagging system including precise robotics and conveyor technology as well as an optical measuring system (ValvoDetect) and an ultrasonic sealing unit (ValvoSeal), complaint and cleaning costs are significantly reduced. The system integrates seamlessly into existing production processes, minimises downtimes during product changeovers and guarantees maximum process and product safety.
Chemical industry
Efficient wax filling system for Reagens Deutschland GmbH
At Reagens Deutschland in Loxstedt, the GREIF-VELOX air packer BVP has drastically reduced cleaning and downtimes when filling micronized waxes and wax mixtures. Thanks to the innovative residual emptying function with optimized bowl shape and air purging system, the cleaning time for product changes has been reduced by 80 percent - from 30 minutes to just 5 minutes. At the same time, less than 12 grams of product remain in the bowl, which means that product losses can be almost completely avoided and the efficiency of the entire filling process is significantly increased.
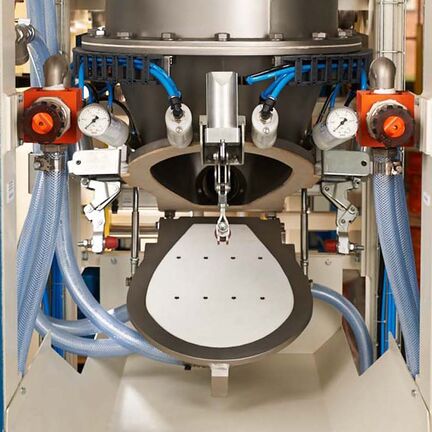
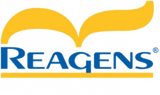
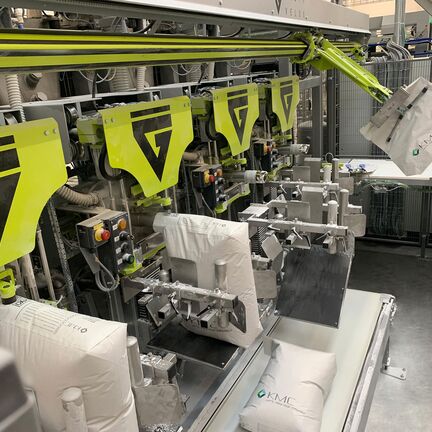
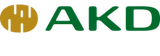
Food industry
Precise valve bag inspection at AKD Toftlund
In this case study, we show how retrofitting the standardized BVPV 4.40 gross pneumatic packer with the ValvoDetect optical sensor system creates decisive quality and efficiency benefits. Two-stage inspection processes (Save & Clean) reliably reject incorrectly opened or incorrectly positioned valve bags before they are filled and sealed. In combination with targeted valve and gluing point optimization, AKD Toftlund reduces bag rejects from the original 0.4-0.8% to just 0.04-0.08%. The result: maximum process reliability, zero complaints and significantly reduced cleaning costs - with a stable throughput rate.
Chemical industry
Powder bagging system at Birla Carbon
Birla Carbon was faced with the challenge of filling ultra-fine, ultra-light carbon black for lithium-ion batteries dust-free, precisely and with uniformly compact bags. With the GREIF-VELOX VeloVac Full-Line in a closed vacuum chamber, it was possible to suck the material directly into the valve bags, recirculate dust and compress the bag volumes by up to 400%. The result: completely dust-free 24/7 operation, increasing throughput rates of up to 33 bags of 102 l per spout and savings of up to 75% in storage and logistics costs - with maximum process and transport safety.
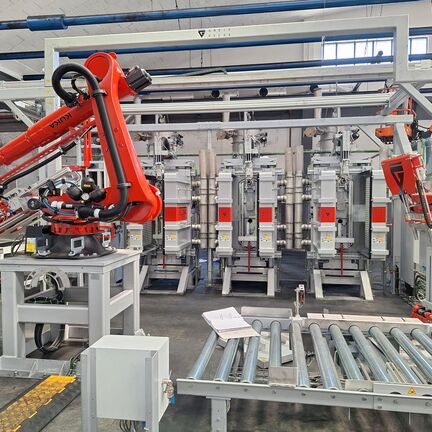
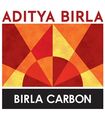
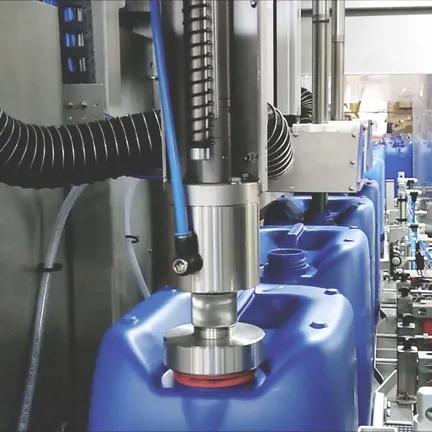
Factory Acceptance Tests (FAT)
Successful handover and installation of GREIF-VELOX systems for customers
Further practical examples of successful factory commissioning of our systems in our customers' production lines are shown in our Factory Acceptance Tests (FAT).