In our full-line systems, all components are perfectly coordinated with each other during the engineering process. This approach enables extraordinary precision and efficiency in filling and bagging, superior to assembled production systems made from individual components from different manufacturers.
As a Kuka system partner, we guarantee highest process reliability and individual solutions that are specifically tailored to the respective requirements and needs of the chemical, petrochemical and food producing industries that fill liquids or solids.
Full-line systems for liquids
Our full-line systems for liquids offer a holistic solution for complex production requirements and material properties from product feeding to final[ -]packaging covers all steps.
Full-line systems optimize the entire filling process, which leads to a significant increase in efficiency. They seamlessly integrate various filling and packaging technologies into a single, coordinated production line, making them ideal for industries that place high demands on precision, automation and safety.
Full-line systems for solids
GREIF-VELOX full-line systems for solids represent production specific and flexible solutions that cover the entire bagging and packaging process from feeding to palletizing.
Our individually configurable full-line systems are perfect for the precise and efficient filling of various solids such as powders and granules, optimizing the production lines and increasing operational efficiency. The modular design allows for quick adaptation to different solids and material properties.
Success factor: project handling, plant development
Every project an individual solution according to a standardized process
We use the stage-gate model to guarantee you structured and efficient project handling. With this approach, each project is guided through clearly defined stages (gates) that are crucial to systematically develop and validate tailored solutions. By using standardized processes within the Stage-Gate framework, we not only ensure the quality and efficiency of each system, but also ensure transparency and traceability in every project phase.
Concept stage
At the beginning, we intensively examine your specific requirements in order to develop a well-founded understanding of your production goals. The concept we create is based on your specifications and includes an optimal system layout, efficient processes and a well-thought-out safety concept.
Design stage
After concept approval, we transform your requirements into a detailed 3D system design. Our engineering team uses advanced CAD tools – and, if desired, 3D scans of your site – to ensure every component of the facility meets your precise requirements.
Production stage
With a strong vertical range of manufacturing, Greif-Velox goes beyond standardized solutions to meet individual customer requirements. Each assembly is subjected to strict quality tests to ensure consistently high manufacturing quality - from procurement to final assembly.
WIBN stage (factory startup)
In this phase, your system at Greif-Velox is fully used for the first time. Through in-depth testing and optimization, we guarantee that all functions work smoothly. The internal Factory Acceptance Test (IFAT), followed by the Factory Acceptance Test (FAT) with you, initiates the successful handover into the assembly phase.
Assembly stage
After detailed planning and production, we deliver the system to your location and carry out the professional assembly and commissioning. This section is rounded off by the Site Acceptance Test (SAT), which confirms the smooth start of your production.
Service stage
Greif-Velox continuously supports you with comprehensive services even after commissioning. Our goal is to ensure the longevity and high performance of your system so that you permanently benefit from maximum productivity and efficiency.
Case studies for
increasing efficiency and flexibility
in production with GREIF-VELOX systems
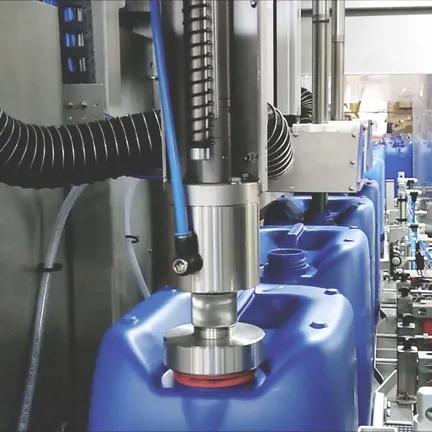
Chemical industry
Hydrogen peroxide filling system for Evonik
Our filling system at the chemical company Evonik led to an impressive increase in filling speed by 50 percent. Additionally, we significantly improved product safety by implementing advanced contamination control measures integrated into a highly automated hydrogen peroxide filling system, increasing not only efficiency but also workplace safety.
Food industry
Bagging system for GoodMills Germany
At the food producer GoodMills Germany, we were able to significantly increase packaging efficiency by 100 percent thanks to our systems. We also maximized the accuracy of the filling processes, doubling production output to up to 400 bags per hour, while at the same time minimizing cleaning effort and changeover times by using our gross pneumatic packer BVPV 4.40.
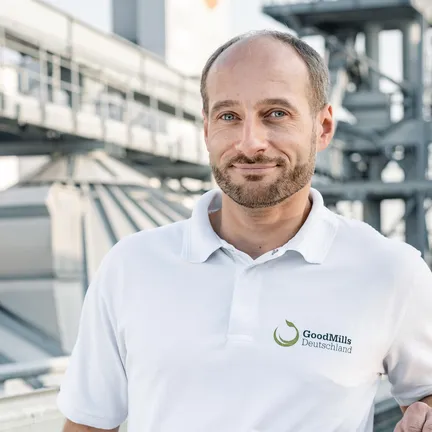
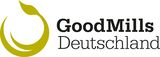
This is GREIF-VELOX: a pioneer of filling and packaging technology in 1,000 years of company history
EIR - Efficiency, innovation, reliability
are the cornerstones of our business philosophy
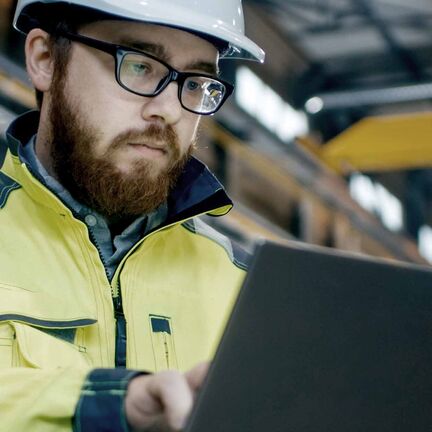
Reduction of operating costs
by reducing transport and logistics costs & saving cleaning and personnel costs
Optimization of production processes
by reducing downtimes, increasing production performance and data-supported process optimization
Improve security and compliance
by increasing employee and product safety
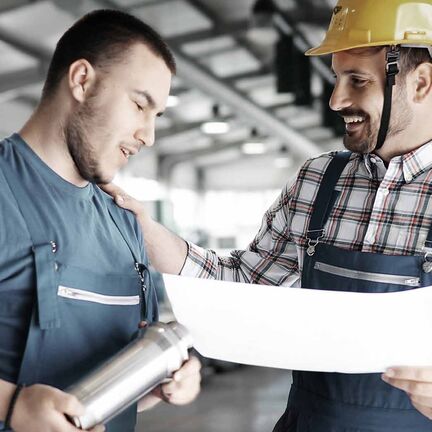
Innovation leadership in the filling and packaging industry
by integrating real-time data collection and Industry 4.0 concepts
Development of customer-specific solutions
through tailor-made adjustments based on specific customer needs, resulting in more efficient production processes
Promoting digital transformation
by using the latest digital tools and platforms for optimized and transparent production, increases productivity and reduces downtime
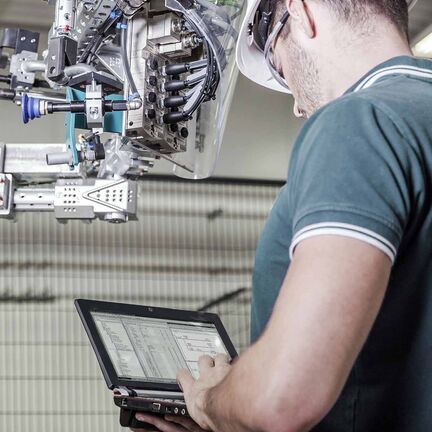
Maximum system availability
through robust design principles and continuous quality controls, resulting in lower failure rates and longer life cycles of the systems
Competent customer support
through rapid technical support & comprehensive maintenance programs, resulting in minimized downtime and optimized operations
Comprehensive security standards
through ongoing training and safety checks, ensures maximum safety for personnel and production

For over 60 years, GREIF-VELOX has been firmly established in the international markets of the chemical, food and petrochemical industries and is valued by customers and partners for its customized filling and packaging solutions, reliability and innovative strength.
Quote: Managing Director Sebastian Pohl
Became the market leader within just a few years
Our experience is reflected in a large number of projects, such as the increase in packaging efficiency at GoodMillsGroup, where we were able to effectively double production output, and the implementation of our ValvoDetect system at ICL Ladenburg, which led to a significant reduction in complaint and cleaning costs.
These and many other case studies demonstrate our ability to respond to a wide range of industry requirements and provide customized, effective solutions. If you would like to see specific examples of our work or gain a deeper insight into our bespoke installations, please contact me directly.
Frequently asked questions about system development
In contrast to many competitors, GREIF-VELOX pursues the strategy in the area of full-line systems that all essential components, including robot programming and the construction of the gripper tools, come from its own company. As a Kuka system partner, GREIF-VELOX has the competence to automate complex processes itself. Thanks to this approach, we combine maximum process reliability and competence with a minimum budget.
Inquiries of this type are part of our daily business: Our retro sales department specializes in inquiries of this type and will be happy to help you. It is not always possible to expand systems from other manufacturers with our innovative additional equipment. We would be happy to consider your concerns on a case-by-case basis. Feel free to send us an email to info@greif-velox.com or use our Contact section on our website.
Whether bagging machines, filling systems, palletizing or entire full lines: Our solutions are not mass production off the assembly line to which the customer has to adapt, but rather individual developments that adapt to customer requirements.
We supply our customers in 89 countries with our filling systems and have direct representation in 15 countries. Please use our contact area to find out about the local representative responsible for you.
The investment budget for a full-line system depends on many individual requirements such as the degree of automation of filling, the type of system and the scope of the desired additional options. In many cases the ROI of the full-line systems we build is significantly less than 20 months.
By using full-line systems, automation components, such as robots for palletizing full containers or even feeding empty containers into liquid systems, have the greatest influence on increasing competitiveness. Automated load securing completes your full-line system. In addition, an automatic connection to your warehouse or a truck loading ramp is even possible.