The customer
At the Weißenstein site in Austria, Evonik employs around 100 people who produce 50,000 tons of hydrogen peroxide (H₂O₂) annually. This is primarily used as a bleaching agent and disinfectant and is also used in medicine and biology. This positions the Weißenstein location as a central gateway to the hydrogen peroxide markets in Austria and Eastern Europe. In addition to H₂O₂, this Evonik plant also produces peracetic acid and polyoxycarboxylic acids, which underlines the chemical company's chemical diversity and technological expertise.
The starting point
A mechanical, semi-automatic filling system has been in operation at the Weißenstein location since the 1980s. “This semi-automatic filling system no longer corresponded to the state of the art in terms of both the level of automation and occupational safety,” says Arnold Sommeregger, factory engineer at Evonik in Weißenstein. “We were under pressure to act.”
The request
In view of the market growth in the peroxide sector and the development of a new business case, Evonik was faced with the challenge of significantly increasing its filling performance. In addition, the new system had to comply with current regulations for employee safety. The chemical industry therefore needed a highly automated filling solution that could efficiently and safely fill hydrogen peroxide into canisters of ten to 60 liters.
In order to meet these requirements, Evonik was looking for a system that had a high level of automation. “It should be automated, from container feeding through filling to labeling, palletizing and wrapping,” explains Arnold Sommeregger. The choice fell on the A-DOS-K full-line system, which was able to fulfill these complex tasks.
The solution
Evonik chose a comprehensive solution from GREIF-VELOX that offered not just a single filling line, but a fully integrated system. “GREIF-VELOX was the only provider who offered us not just the filling system, but a coordinated complete system, with one contact person for the entire system. That's why we decided on the A-DOS-K," explains Arnold Sommeregger.
The chosen system, the A-DOS-K-Full-Line, maximizes performance while ensuring employee safety. It is able to fill up to 240 canisters per hour fully automatically. These canisters can contain low to medium viscosity products and are processed within a seven-stage safety system, significantly increasing the efficiency and safety of filling processes.
The seven-stage security system
- Automatic attachment, capture and checking of labels (data)
- Checking the containers based on their tare weight
- Calibrated filling and bunghole extraction directly at the emission source
- Automatic shutdown in the event of overfilling and leaks
- Safe automatic closing process with documentation of the torque and screw-in depth
- Automatic palletizing and load securing without damaging the canisters
- Automated cleaning of the system for product changes
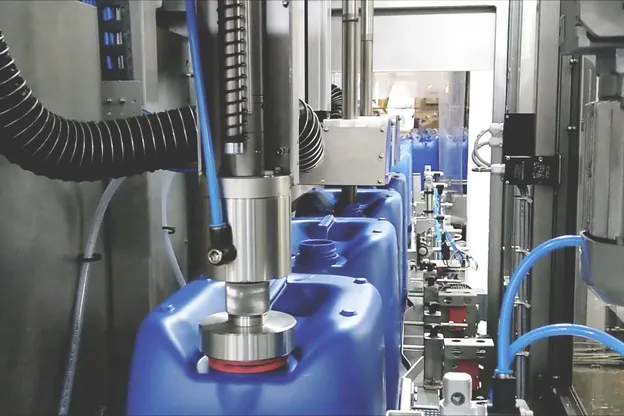
The result: breakthrough in productivity and safety at Evonik
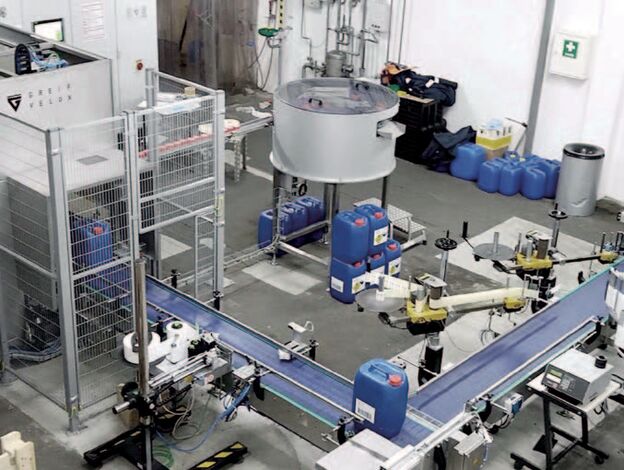
By implementing the GREIF-VELOX filling system A-DOS-K, Evonik Weißenstein was able to significantly improve its filling performance: 200 30-liter canisters can now be filled automatically per hour, which corresponds to an increase in filling performance by 30 percent. The entire filling and closing process takes place in containment, which prevents employees from coming into direct contact with the chemicals and protects both the environment and product purity. Multiple security checks increase occupational safety as well as loading and transport safety.
The integration of the system into the existing control system enables smooth data exchange, whereby all relevant process data is automatically recorded and processed. This not only makes complaint management easier, but also improves quality assurance. “No other manufacturer was able to implement the overall package as flexibly as Greif-Velox,” emphasizes Arnold Sommeregger. “Now we have a completely digitalized process.”
In addition, the follow-up support from GREIF-VELOX is impressive: If adjustments are required or problems arise, the remote support team offers quick and effective solutions by working directly with local experts to optimize system performance.
We really like the fact that GREIF-VELOX is a medium-sized company with a high level of in-house production, which means that the aftercare, including spare parts management, also works perfectly.
Arnold Sommeregger
Plant engineer at Evonik in Weißenstein
30 percent higher filling performance
Highest possible employee and product safety
Saving personnel costs
Reduction in complaints
Cost savings through continued use of existing production systems
Reduction of downtimes through reliable and fast all-round service (with remote connection)