The customer

ICL Ladenburg, also known as BK Giulini GmbH, is a fully integrated subsidiary of the ICL Group based in Tel Aviv, Israel. At the Ladenburg location, the company employs around 450 people who focus on the development, production and distribution of additives for the food industry. These additives are primarily used in the production of high-quality foods. In addition, ICL Ladenburg offers products for technical applications that are used as basic materials in cleaning agent production, metal surface treatment, as well as technical additives for varnishes and paints and as additives in the cosmetics and construction industries.
The starting point
At the Ladenburg location in Baden-Württemberg, ICL recorded annual complaints and cleaning costs of at least 20,000 euros. These costs were mainly due to individual bags that were not properly sealed. The resulting product leakage led to the contamination of entire pallets, which in turn resulted in increased cleaning costs and customer complaints.
The request
Operations manager Thomas Jörder was faced with the challenge of significantly reducing the complaint and cleaning costs caused by incorrectly welded bags. "The evaluation of a product with top quality must not fail because of a contaminated pallet "," emphasized Jörder. He needed a reliable solution to ensure the integrity of the packaging and therefore product quality.
He therefore looked for an effective control mechanism in the food and chemical industries. The choice fell on the GREIF-VELOX ValvoDetect for the BVP air packer, developed by the GREIF-VELOX development team to precisely identify and prevent errors when welding the bags.
The solution
The GREIF-VELOX team identified the causes of the inadequate welding of the bags at ICL Ladenburg. It turned out that deviations from the standard or incorrect settings of the bag chair resulted in bags being placed crookedly on the valve connectors. This caused incomplete seals from which product leaked and contaminated the pallets.
Based on these findings, GREIF-VELOX developed ValvoDetect, a special feature for the BVP air packer that identifies and sorts out defective bags before they reach the pallet. This is made possible by the use of two optical sensors, which check whether the bag valve is correctly positioned in relation to the welding sonotrodes before the welding process. If this is not the case, the bag is ejected directly. Depending on the setting, the operating personnel can stop the machine to make readjustments or simply record the irregularities statistically.
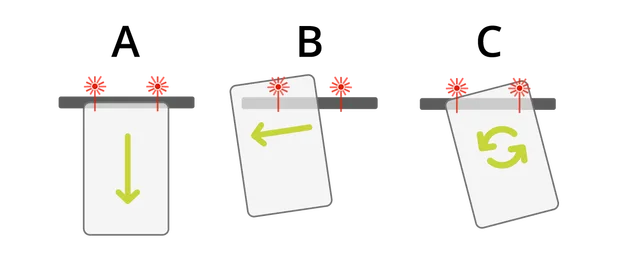
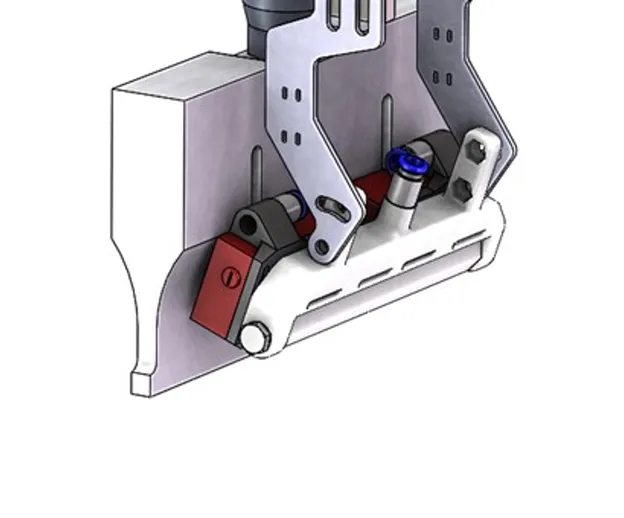
The result: savings and increased customer satisfaction at ICL Ladenburg
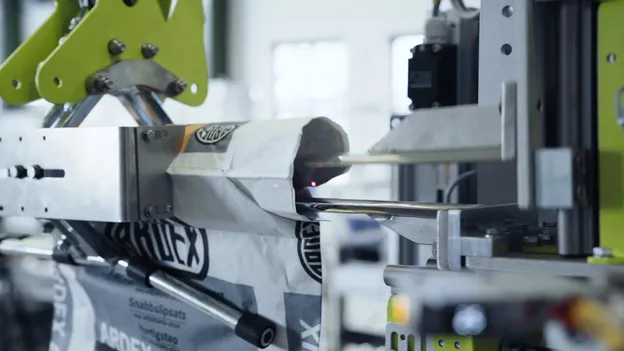
By integrating the GREIF-VELOX ValvoDetect together with the BVP air packer, ICL Ladenburg was able to save around 20,000 euros in complaint costs annually and significantly reduce the effort in complaint management. Other users have reported that they have been able to recover significant amounts thanks to the reduction of the bag error rate to 0.5 percent - including €9,000 from bag manufacturers for complaints and an additional €8,000 in saved cleaning costs.
Operations manager Thomas Jörder summarizes the advantages of ValvoDetect and describes it as “absolute added value” for the company. “The bottom line is that we obviously have even more satisfied customers and a better brand reputation,” emphasizes Jörder. This highlights the effectiveness of the solution not only in reducing costs, but also in improving customer relationships and strengthening brand integrity. .
GREIF-VELOX ValvoDetect is an absolute added value for our company. The bottom line is that we have even happier customers and a better brand reputation.
Thomas Jörder
Operations manager at ICL in Ladenburg
30 percent higher filling performance
Highest possible employee and product safety
Saving personnel costs
Reduction in complaints
Cost savings through continued use of existing production systems
Reduction of downtimes through reliable and fast all-round service (with remote connection)