Our specialized robot palletizing systems can be seamlessly integrated into existing production lines or can be developed as part of a full-line system.
They combine advanced technologies with flexibility to ensure efficient handling of different container types and sizes.
High performance in robot palletizing
Reliably palletize 2000 bags per hour.
VeloPack - highly efficient robot palletizing
Our globally proven robot palletizer VeloPack automates and simplifies palletizing through the use of innovative robot technology.
This system offers solutions for both palletizing and depalletizing drums, hobbocks and canisters as well as sacks and buckets, offering flexible configuration options from 4-axle to 6-axle versions and a load capacity of up to 400kg.
VeloPack allows multiple lines to be palletized at the same time and can be equipped with additional gripping tools for pallet and cover sheet handling, making it particularly adaptable and efficient.
Multiple palletizing: Allows products from different production lines to be palletized at the same time.
Flexibility: Supports 4-axis to 6-axis robots for different handling tasks.
Load capacity: Can handle loads of up to 400kg, ideal for heavy and large-volume products.
Additional options: Available with dedicated pallet and cover sheet gripping tool to simplify handling and increase throughput.
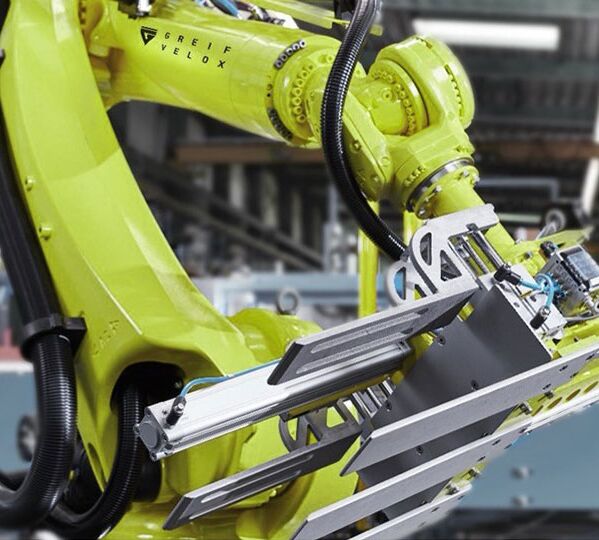
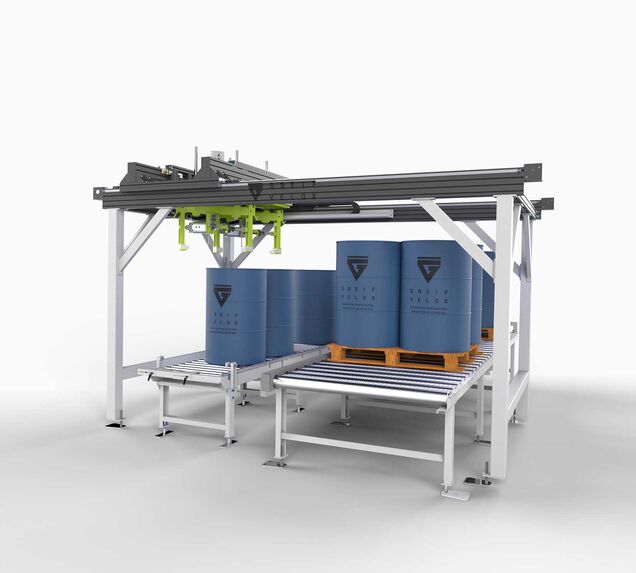
Portal palletizer - automatic palletizing for the highest demands
The portal palletizer is a fully automatic solution that was specifically developed for the demanding palletization of drums, hobbocks and canisters.
It can be combined with all elements of conveyor technology and can be designed as a palletizer with gripping tool, vacuum palletizer or push palletizer to ensure seamless integration into the production line.
Versatility: Can be designed as a grip, vacuum or push palletizer depending on the specific needs of the production line.
Integration: Can be seamlessly integrated into existing conveyor technology systems, allowing implementation into existing production environments.
Automation: Fully automatic system that simplifies operation and increases production efficiency.
Vorteile der Produktionsautomatisierung mit GREIF-VELOX-Roboterpalettierern
Erfolgsfaktoren für Chemie-, Petrochemie- und Lebensmittelbranche
Clean
GREIF-VELOX robotic palletizing systems use precise handling techniques that minimize contact between products and the environment to avoid contamination and ensure product quality throughout.
Automatically
The fully automated processes within palletizing processes reduce the need for manual intervention, increase the efficiency of the final packaging processes and increase operational safety.
Efficient
The automation and advanced robotics within GREIF-VELOX palletizing systems maximize production speed while reducing waste and operational costs.
Secure
Integrated safety features in every robotic palletizing system protect both operators and products, ensuring compliance with strict, production-specific industry standards.
Sustainable
GREIF-VELOX integrates environmentally friendly technologies into its palletizing systems that reduce energy consumption and increase efficiency while improving the reusability of resources.
Specific
GREIF-VELOX develops tailor-made robotic palletizing solutions that are precisely tailored to the specific requirements and needs of customers from the chemical, petrochemical and food industries.
Precise
Advanced control technologies enable GREIF-VELOX palletizing robots to handle and position products with exceptional accuracy.
Flexible
The modularity and adaptability of the robot palletizers process different product and container sizes with minimal changeover times, resulting in the fastest possible changes between different production runs.
Integration of GREIF-VELOX robot palletizers into existing production environments
The GREIF-VELOX robot palletizers are specifically designed for smooth integration into existing production lines, which enables efficient and problem-free integration into our customers' existing processes.
Especially in combination with our flexible and efficient pallet filling systems for liquids, production companies create optimal palletizing solutions for their industry.
Pallet filling systems for liquids in detailThe VeloPack system for palletizing or depalletizing offers the flexibility to function both as part of a full-line system or as a standalone unit through adjustments in design and configuration. This modularity ensures easy adaptation to different production requirements and container sizes.
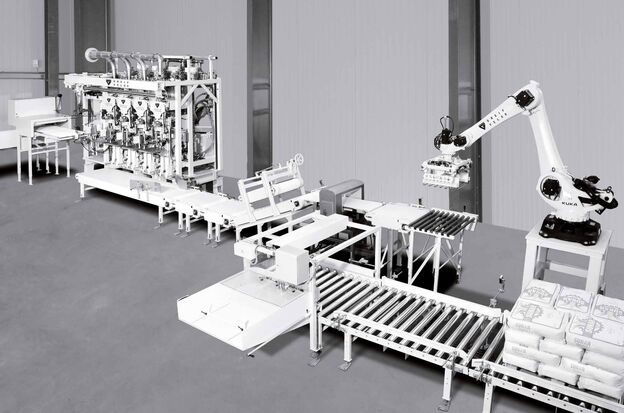
Holistic system solutions
Complete systems instead of individual machines, which simplifies integration.
Modular design
Flexible adaptation and expansion of the systems to the existing production lines.
Scalability
Easy adaptation to changing production volumes and different container sizes.
Increased efficiency
Seamless integration increases operational reliability and minimizes downtimes.
One contact person
for your entire project.
Empty pallet handling
The robot can also help with handling empty pallets. If a separate solution is desired, GREIF-VELOX can offer external empty pallet magazines with and without film applicators. It is possible to access different palletizing locations in one line.
Sack equalization
For good palletizing results with bags, they must first be shaped. This means that the bulk material contained is distributed evenly throughout the bag. We offer various solutions for this process. These include ironing belts, vibration plates, pressing stations and torture lines.
Cover sheet handling
Cover sheet handling can be achieved using a robot gripper tool or using separate components. GREIF-VELOX offers external cover sheet dispensers and film applicators.
Pallet conveyor technology
GREIF-VELOX provides pallet conveyor technology systems for the removal and further transport of the pallets. Roller conveyors, chain conveyors, corner transfers, turntables or pallet lifts complete the program.

For over 60 years, GREIF-VELOX has been firmly established in the international markets of the chemical, food and petrochemical industries and is valued by customers and partners for its customized filling and packaging solutions, reliability and innovative strength.
Quote: Managing Director Sebastian Pohl
Became the market leader within just a few years
Our experience is reflected in a large number of projects, such as the increase in packaging efficiency at GoodMillsGroup, where we were able to effectively double production output, and the implementation of our ValvoDetect system at ICL Ladenburg, which led to a significant reduction in complaint and cleaning costs.
These and many other case studies demonstrate our ability to respond to a wide range of industry requirements and provide customized, effective solutions. If you would like to see specific examples of our work or gain a deeper insight into our bespoke installations, please contact the appropriate contact person.