Greif-Velox Safe Operation Gate: Greatly increased efficiency for manually operated valve bag filling systems
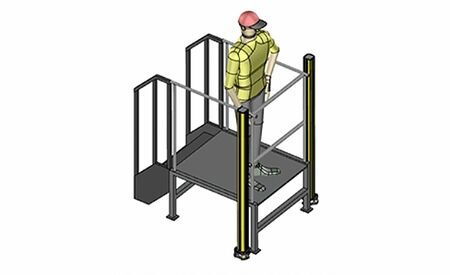
Maximum worker safety and optimised ergonomics for the manual operation of valve bag filling systems: in combination with an ascending conveyor belt, Greif-Velox’s Safe Operation Gate increases efficiency by around 40 percent and greatly reduces labour costs.
Manual operation of most valve bag filling systems reduces efficiency and ergonomics for two reasons.
Firstly, the European Machinery Directive (2006/42/EC) and the general design principles according to DIN EN ISO 12100 stipulate that if an employee operates machines with moving parts on open devices, as is the case with semi-automatic valve bag filling systems with automatic welding, he must be stationary so that he is protected from interfering with a dangerous movement.
The classic solution for this is an electrical two-handed operation, where both control elements must be operated synchronously so that operation can begin.
However, this means reduced efficiency: the employee cannot carry out any further work during operation.
On the other hand, there is another disadvantage: after the bag has been successfully filled and welded, the operator must manually place it on the a pallet or conveyor belt. Depending on the filling weight of between 10 and 50 kilograms, this means a great physical strain for the employee, especially when a large quantity is filled per hour.
The solution from GREIF-VELOX
In order to make the workplace particularly ergonomic for employees, Greif-Velox has developed a solution that simultaneously protects employees and increases productivity: the Greif-Velox Safe Operation Gate.
The feature consists of a protective fence that ensures the necessary safety distance between the machine and the operator. On the other hand, a safety light curtain in the access area of the machine ensures that the machine does not start if a person or object is in the danger zone. This means that the operator does not have to use two-handed control during the filling time, but can instead carry out other activities such as packaging and set-up work.
A conveyor belt makes the employee's work easier when he has to place the filled bags on the pallet or a conveyor belt.
Concrete added value from the Safe Operation Gate
With a two-handed operation time of ten seconds per bag and an output of 200 bags per hour, the Safe Operation Gate can convert around 25 minutes of inactive waiting time per hour into active working time. For an eight-hour shift, this corresponds to an efficiency increase of 40 percent.
With four-shift operation and wage costs of 40 euros per hour, this results in savings of more than 100,000 euros per year.