Safe and clean carbon black bagging for the electromobility transition
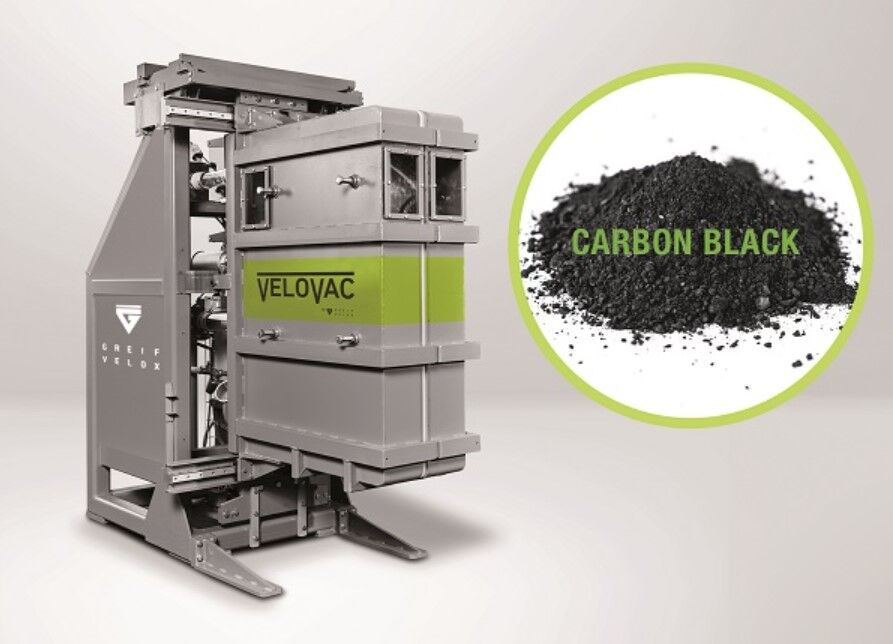
Greif-Velox VeloVac XL in the cav: Dust-free filling of carbon black in FIBCs
Dusty and difficult to handle, but indispensable for many industries: carbon black is essential for the manufacture of products such as tires or lithium-ion batteries - and is therefore also particularly important for future industries such as electromobility. However, the ultra-light powder poses a major challenge for manufacturers - not least as a potential source of danger in the workplace. Greif-Velox has the solution: the market-leading and innovative VeloVac vacuum packers ensure dust-free, clean and safe bagging of these difficult-to-handle products.
Bagging carbon black: usually a dirty business
Manufacturers of carbon black are usually faced with major problems when using conventional bagging methods such as pump packers: heavy contamination of the plant environment with high cleaning costs, extensive logistics and complaint costs due to contaminated bags and an increased risk of danger for employees due to the harmful dust. The bags and pallets themselves can also be contaminated, which leads to additional cleaning and quality costs and can damage the brand's reputation.
Greif-Velox VeloVac: Dust-free and safe for a high-purity product
Greif-Velox solves these problems: VeloVac technology makes the bagging process of ultra-light powders completely dust-free in a sealed vacuum chamber. Other functions such as the intelligent aspiration functions and the powerful Greif-Velox ValvoSeal ultrasonic sealing unit ensure a continuous process and safe handling. To ensure that neither the bag nor the pallet is contaminated, a cutting device in the system automatically cuts off any valve overhangs that may still contain product residues. This ensures a clean working environment for the operator and prevents additional product loss. The combination of the various features results in a high-purity product that is required for battery production. This is because metallic impurities and moisture can lead to undesirable side reactions and have a negative impact on the performance and shelf life of the battery.
Reduced CO2 footprint: savings on transportation and logistics costs
The vacuum process also compacts the product during bagging. The result is uniformly shaped, easily stackable bags without air pockets. This ensures a uniform, clean pallet appearance. By using vacuum technology, carbon black producers can reduce the shipping volume by more than 50% and thus also massively reduce logistics costs. This also reduces the CO2 footprint during transportation.
Greif-Velox VeloVac XL: Efficient bagging in FIBCs
With the innovative VeloVac XL gripping Velox system, manufacturers can now also fill FIBCs ("big bags") using the vacuum method and benefit from the same advantages as the VeloVac system for smaller containers. In addition to the high savings potential in terms of efficiency, cleanliness and employee safety, there are additional effects from reduced storage, logistics and quality costs. Thanks to the almost 70 times higher capacity of FIBCs with a capacity of 200 to 230 kilograms compared to the much smaller valve bags, end customers can process and empty the larger bags more quickly and save up to 30 percent on packaging material.
Available faster and more sustainably: Carbon black for the electromobility transition
Carbon Black's optimized filling and packaging process using vacuum technology ensures that the high-quality material is made available to the end customer in larger quantities more quickly and in perfect packaging. The process reduces the CO2 footprint of battery production and thus sustainably supports the electromobility transition.
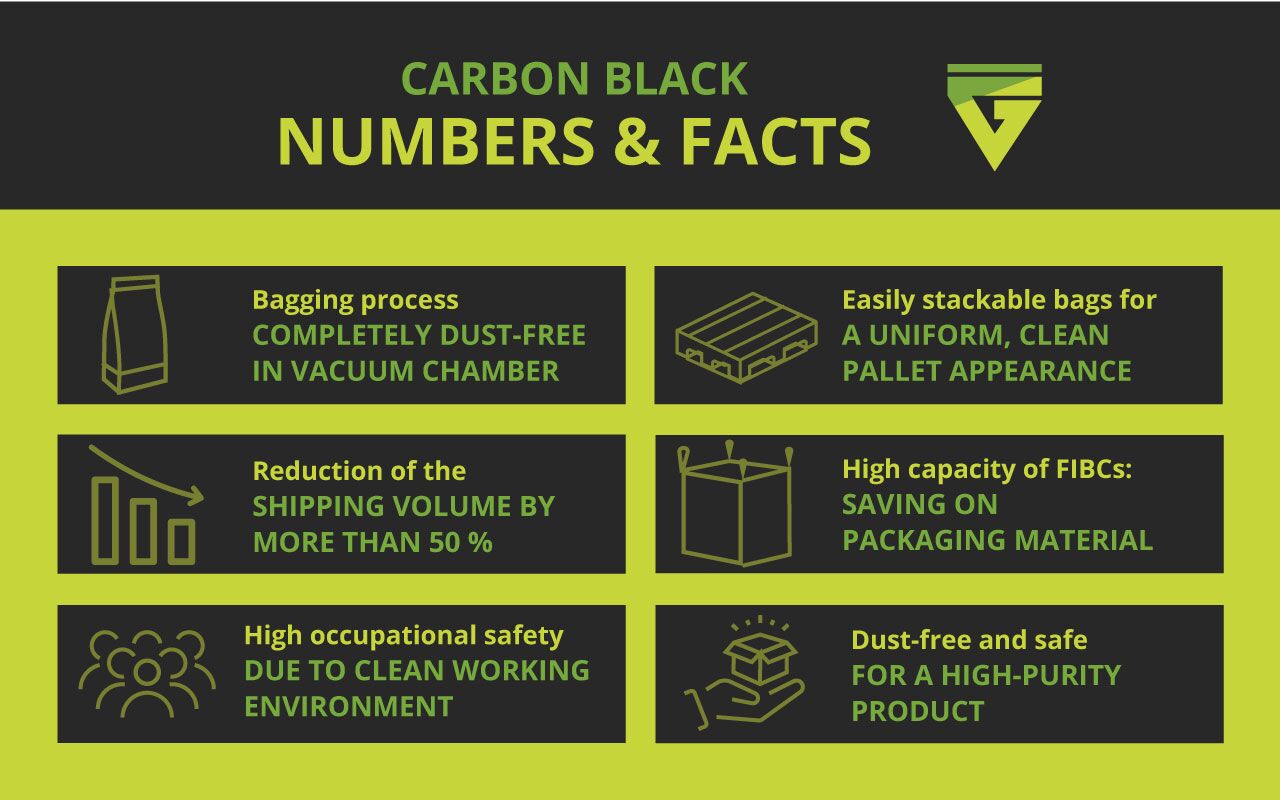
Carbon Black: Ultralight powder with exceptional properties
Carbon black is a paracrystalline carbon material characterized by an above-average surface-to-volume ratio. It has a very small grain diameter of 60 to 110 nanometers as well as a low bulk density and high air absorption capacity. Carbon black is mainly used as a pigment and as a reinforcing agent in car tires. It also performs the function of dissipating heat from the tread and belt area of the tire, reducing thermal damage and extending the life of the tire. Carbon black is also a widely used component in cathodes and anodes and serves as a safe alternative to lithium metal in lithium-ion batteries. Approximately 20 percent of global production is accounted for by the manufacture of belts, hoses and other rubber-based products unrelated to tires. The remaining 10 percent is used as a pigment in inks, coatings and plastics and as a conductive additive in lithium-ion batteries as an essential component of electric vehicles.