Revolutionising production processes: With intelligent networking to smart industry
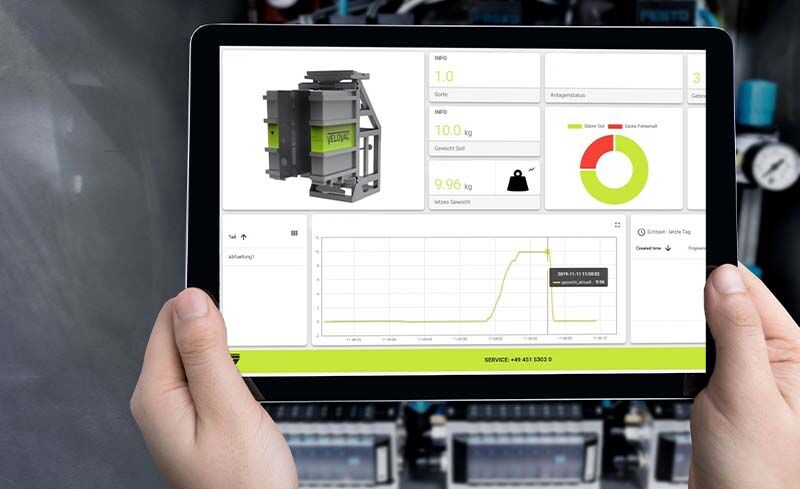
Decreasing storage capacities and the order-related individualization of products and product batches place high demands on both the production and packaging process. Maschinenfabrik Greif-Velox therefore develops packaging systems that are individually tailored to customer requirements, which organize themselves and optimize processes thanks to intelligent networking. This brings clearly measurable benefits for planning, production, logistics and maintenance.
The use of sensor-monitored, cyber-physical systems fundamentally changes production and packaging processes: Based on the data collected, the process control system itself decides which filling of which substance in which quantity would currently be optimal and sends the information directly to the system via the merchandise management system.
Reduction of downtimes, saving of storage capacities
All system messages and machine parameters, such as current weights, number of bags, current pressures or torques, are recorded by sensors and, thanks to a flexible data interface, can be collected in a cloud and networked with the customer's process control system. In such a completely digital process, downtimes due to sub-processes that are not correctly timed can be avoided. Storage capacities are also saved if the process is coordinated with the transport logistics in such a way that the product is collected directly after production. Greif-Velox reacts flexibly to the user's requirements when setting up the system, so that existing components can be supplemented and costs can be saved when integrating them into the overall system.
In future, the data from the filling and packaging process will be clearly displayed on a dashboard, allowing system operators to obtain an overview of the system's performance at any time and from any location via a secure VPN connection and also to intervene in the production process.
Increasing efficiency through predictive maintenance
Increasing productivity through intelligently networked components also includes the further development of predictive maintenance, i.e. proactive maintenance. By recording and evaluating time-, cycle- and condition-based data, the system can inform the user in good time before a potential failure occurs, e.g. that a system component needs to be replaced. In this way, downtimes in the production process can be minimized and machine utilization can be optimized. "Overall, customers benefit from higher output and increased efficiency," says Benjamin John, Director of Engineering at Greif-Velox.