GREIF-VELOX transforms production technology
Our highly automated filling and packaging systems overcome the production hurdles of large, globally active companies
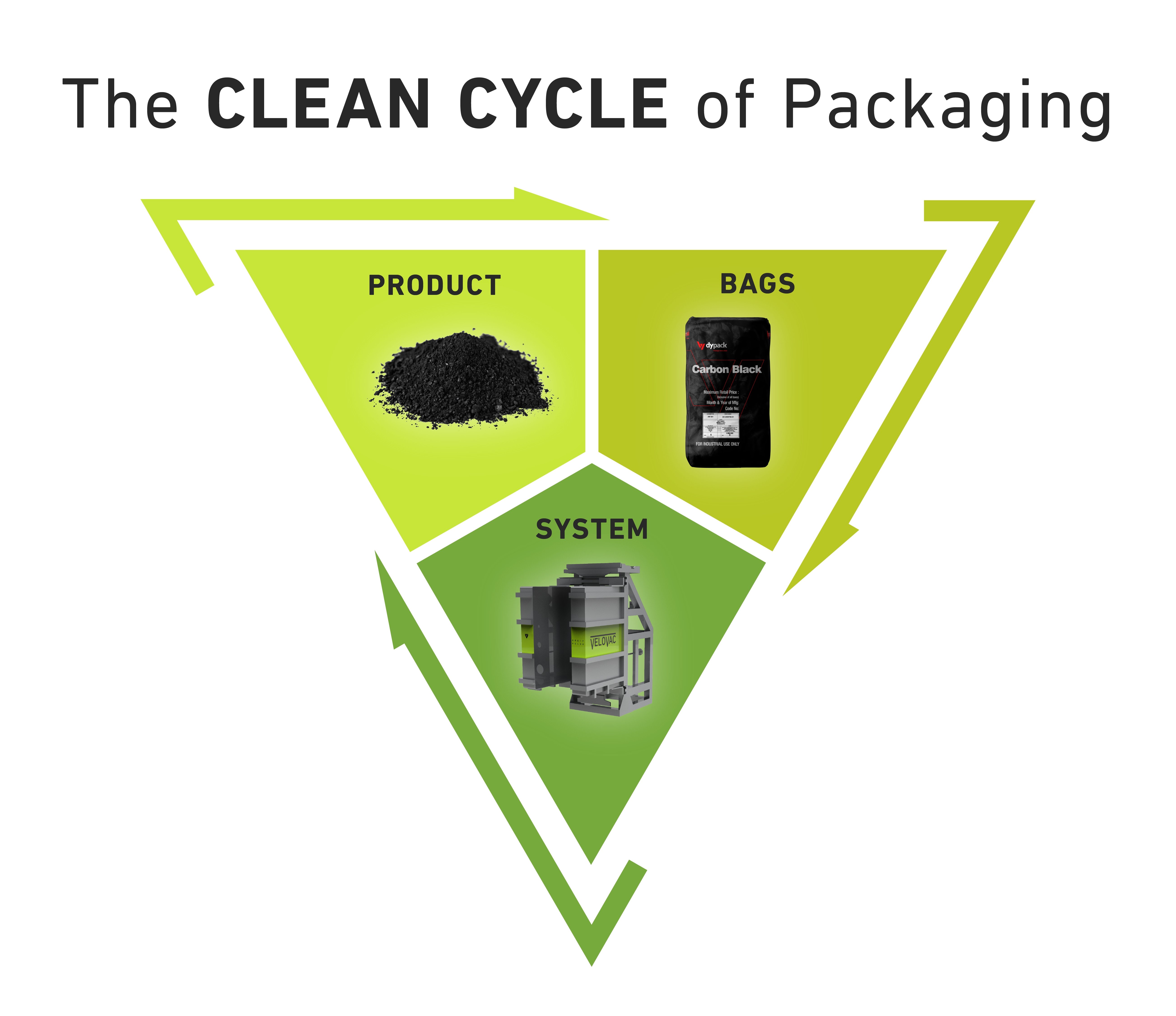
More flexible
Our modular filling systems enable quick adaptation to different product types and container sizes, enabling seamless switching between different production lines and a significant reduction in changeover times.
More sustainable
By introducing energy-efficient systems and sustainable production processes, our facilities reduce the carbon footprint and promote the reusability of resources, which is anchored in our latest facility designs.
More efficient
With innovative filling technology, we increase filling speeds by up to 50 percent or double the output capacity of bags per hour.
Cleaner
By using our VeloVac technology, we enable dust-free bagging processes that not only improve the working environment, but also significantly reduce environmental impact.
Safer
Our specially developed safety and cleaning functions and advanced contamination protection measures increase workplace safety many times over and set new standards in production hygiene.
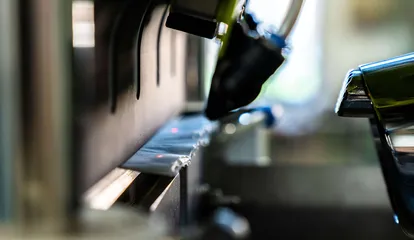
Case study:
ICL Ladenburg
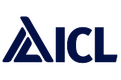
Significant reduction in complaint and cleaning costs Improvement in end customer satisfaction and brand reputation.
ICL Ladenburg belongs to the food and chemical industry. The company operates production facilities for food and beverages as well as for technical applications and develops, produces and sells additives for the food industry and industrial applications, including additives for cleaning agent production, metal surface treatment, technical additives for varnishes and paints as well as for the cosmetics and construction industries.
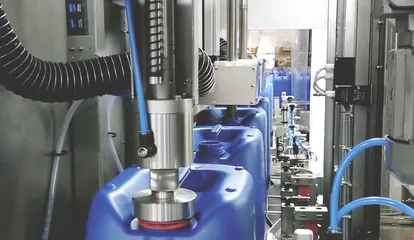
Case study:
Evonik
Increase filling speed by 50 percent Improve product safety through advanced contamination protection measures.
Evonik belongs to the specialty chemicals industry. Its product portfolio ranges from high-performance materials to additives for various industries, including hydrogen peroxide, an essential ingredient in bleach production and disinfection.
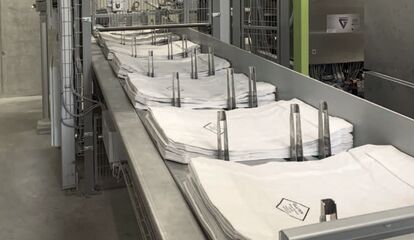
Case study:
GoodMills Deutschland
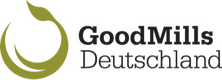
Doubling packaging efficiency and production output to up to 400 bags per hour. Minimization of cleaning effort and changeover time.
GoodMills Germany belongs to the food industry and is one of the leading milling companies in Europe. Specializing in the production of high-quality flour and semolina for bakeries, food processors and the beverage industry, GoodMills places particular emphasis on product quality, efficiency and sustainability in its production processes.
Success factor: project handling, plant development
Every project an individual solution according to a standardized process
We use the stage-gate model to guarantee you structured and efficient project handling. With this approach, each project is guided through clearly defined stages (gates) that are crucial to systematically develop and validate tailored solutions. By using standardized processes within the Stage-Gate framework, we not only ensure the quality and efficiency of each system, but also ensure transparency and traceability in every project phase.
Concept stage
At the beginning, we intensively examine your specific requirements in order to develop a well-founded understanding of your production goals. The concept we create is based on your specifications and includes an optimal system layout, efficient processes and a well-thought-out safety concept.
Design stage
After concept approval, we transform your requirements into a detailed 3D system design. Our engineering team uses advanced CAD tools – and, if desired, 3D scans of your site – to ensure every component of the facility meets your precise requirements.
Production stage
With a strong vertical range of manufacturing, Greif-Velox goes beyond standardized solutions to meet individual customer requirements. Each assembly is subjected to strict quality tests to ensure consistently high manufacturing quality - from procurement to final assembly.
WIBN stage (factory startup)
In this phase, your system at Greif-Velox is fully used for the first time. Through in-depth testing and optimization, we guarantee that all functions work smoothly. The internal Factory Acceptance Test (IFAT), followed by the Factory Acceptance Test (FAT) with you, initiates the successful handover into the assembly phase.
Assembly stage
After detailed planning and production, we deliver the system to your location and carry out the professional assembly and commissioning. This section is rounded off by the Site Acceptance Test (SAT), which confirms the smooth start of your production.
Service stage
Greif-Velox continuously supports you with comprehensive services even after commissioning. Our goal is to ensure the longevity and high performance of your system so that you permanently benefit from maximum productivity and efficiency.
Certified quality. Sustainable responsibility.
As an ISO 9001:2015 and ISO 14001:2015 certified company, GREIF-VELOX stands for reliable quality and responsible action. Our internal processes are consistently geared towards efficiency, safety and customer satisfaction - verified by independent audits.
At the same time, we take responsibility for the environment: our certified environmental management system ensures that we conserve resources, minimize emissions and develop sustainable solutions in packaging technology.
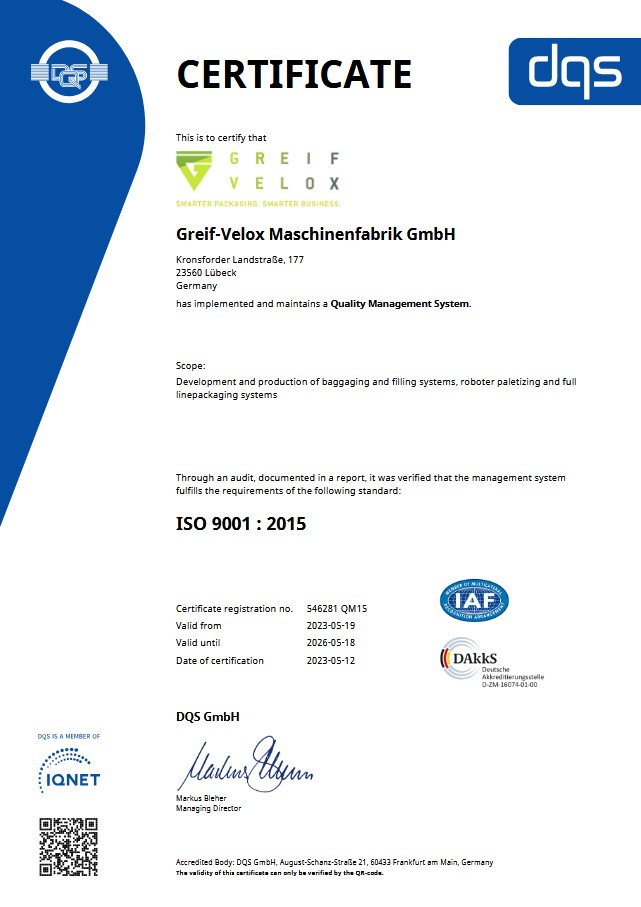
Certificate ISO 9001
download PDF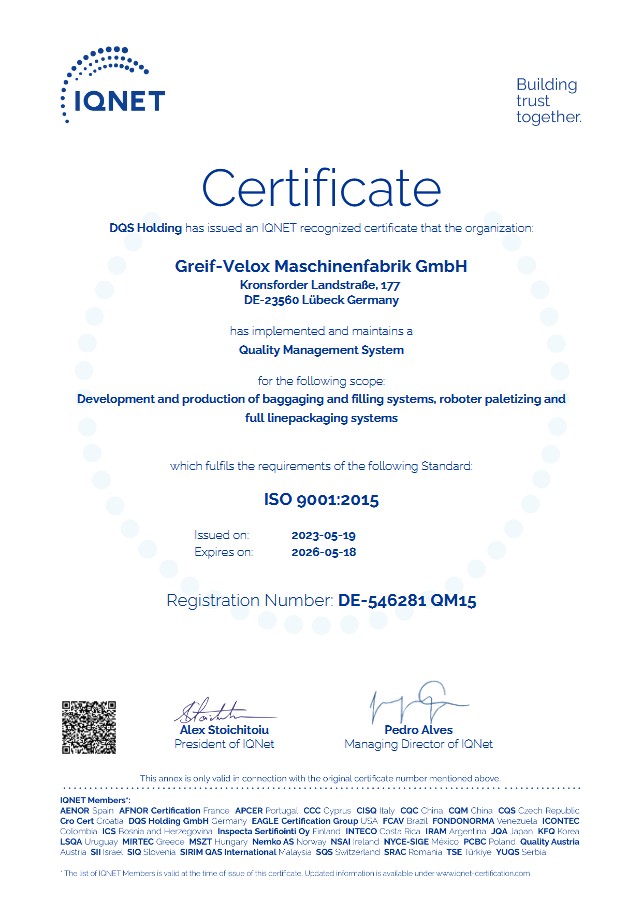
Certificate IQNet ISO 9001
download PDF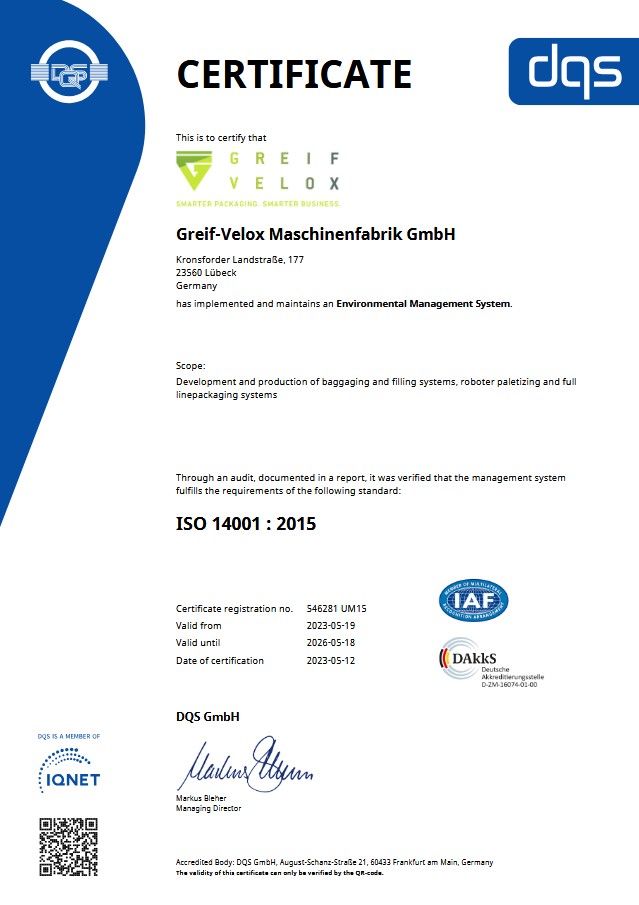
Certificate ISO 14001
download PDF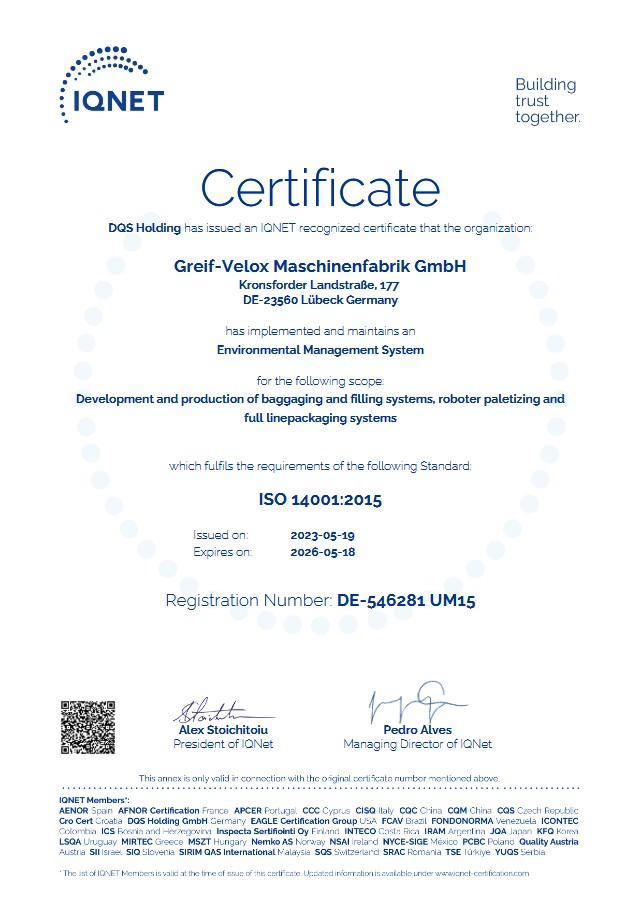
Certificate IQNet ISO 14001
download PDFCompany structure & markets
Global business. Worldwide service. In more than 89 countries.
4 key departments
at the company headquarters in Lübeck
Administration & coordination
At the heart of our processes in Lübeck lies administration, the backbone of Greif-Velox, which includes all back office activities and the entire coordination of the various units. Under the leadership of the management, this area ensures an efficient connection between departments such as HR and Finance and the operational units such as Service and Realization.
Implementing state-of-the-art collaboration tools ensures that all projects are efficiently recorded, documented and planned with the highest level of transparency, providing our customers with clear and understandable insight into project execution.
Sales & Consulting
Our sales engineers are more than just the first point of contact for our customers; They are experts who will support you from the first inquiry to the final implementation.
Specializing in light, solid and liquid filling, they offer comprehensive advice and, with the support of our Innovation & Application team, design individual system solutions that are not only tailored to your specific needs, but also give you significant market advantages. Our engineers focus on developing tailor-made, future-oriented solutions that make your operations more efficient and profitable.
Service & Installation
The Greif-Velox service team combines technical expertise in mechanics, electronics and software to directly meet a wide range of customer requirements. Involved from the initial concept phase, our technicians know every detail of your project, ensuring efficient and knowledgeable installation and comprehensive support.
With the latest service tools and technologies, including advanced VPN solutions, our team not only enables optimal commissioning, but also provides long-term support with upgrades, optimizations and spare parts management.
Construction & Realization
In this department, our engineers and designers work hand in hand to develop precise and effective filling solutions. In close collaboration with the Innovation & Application Department, individual and innovative solutions are created that redefine the standards of the industry.
Our project management team guarantees a transparent and efficient process from planning to final implementation, focusing on minimal expenses for our customers while maintaining the highest quality standards.
We offer you service every day.
we process annually.
we have been delivering so far. Ascending trend.
This proportion of our customers always inquire about future projects with us.
We employ people worldwide at Greif-Velox.
we have realized so far.
and parts list are in our ERP system.
Our annual production of air packers may drop.
From the Greifen mill to the market leader
1000 years of company history
1100
Monks founded the Greifen Mill in Klützow.
1399
Sale of the mill and the village to the priest vd Zinne for the benefit of a spiritual foundation.
1409
Gradual transition of the mill into the private assets of the vd Zinne family.
1734
Johann Mahlkuch runs the mill and expanded it over the years.
1852
Expansion of the mill according to the innovative "American system" to produce very fine, more expensive flour.
1865
Reconstruction and technical expansion of the mill to include turbines and steam engines.
1891
The mill burns down due to a hot wooden shaft bearing and is immediately completely rebuilt with new machines.
1908
Ernst Mahlkuch, owner of the mill, patented the first calibratable automatic bagging scale in the year of his master craftsman examination.
1914
Because of the beginning of the First World War, the mill had to give up six horses and several employees. She also joins the newly founded Reichsgraidestelle for profit.
1920
Intensive expansion of the mill and mill storage as well as the purchase of electric limousines.
1921
New patent applications for an automatic bag packing scale and a bag elevator.
1934
The mill was completely rebuilt due to a major fire in 1933. With various improvements and innovations by the owner, inventor Ernst Mahlkuch.
1938
After registering several patents in weighing and bagging technology, the Greif factory was founded and built in Klützow.
1941
The Greif factory is being expanded significantly due to the high demand for its bagging machines.
1945
Greif-Werke is founded in Lübeck.
1978
Takeover by the Möllers Group.
1997
Renaming of Greif-Werke to Greif-Velox.
1999
Takeover of the Logdos company (liquid bottling).
2012
Greif-Velox produces high-quality, individual full-line systems.
2018
The Greif-Velox management team, together with the investment company BPE, is taking over all shares in the company.
News & Publications
Well informed and up to date
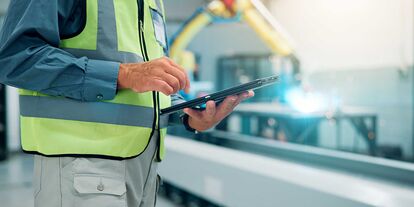
Faster service, less downtime: The Greif-Velox spare parts portal enables digital, intuitive ordering directly from the machine view.
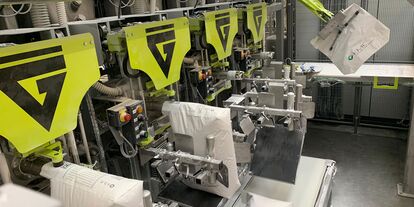
Detecting and Removing Faulty Bags with ValvoDetect.
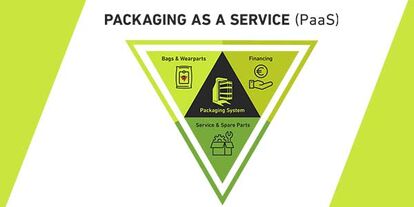
Maximum efficiency, full cost control, and reliable supply: With our new PaaS model, we are simplifying industrial powder bagging like never before.
Career at Greif-Velox
Are you looking for a job in which you can realize yourself and make full use of your skills? Then we have the right workplace for you! We at Greif-Velox are visionaries, partners, teachers and learners – and of course an unbeatable team. In addition to groundbreaking bagging machines and filling systems, we work every day to create a positive working atmosphere - for example through flexible working time models, attractive salaries and employee events. Because we know: Only those who enjoy working in their team can fully exploit their potential.
We are a company with 1,000 years of history that consistently looks forward: In addition to efficiency and reliability, innovation is clearly one of the values that drive us forward. Whether in the technical or commercial area or as a trainee – be there! Start your career at Greif-Velox now.
And if your position cannot be found here, we look forward to receiving your unsolicited application.
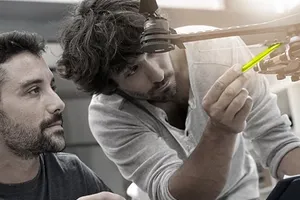
Technical Jobs
From electronics technicians and engineers to IT experts – you can find job advertisements in the technical area here.
learn more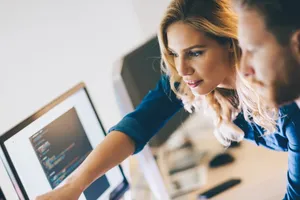
Commercial professions
From office management to controlling and administration: our commercial jobs are here.
learn more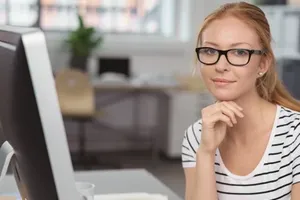
Education
Electronics technicians, mechatronics technicians, mechanics, business people - we provide training.
learn more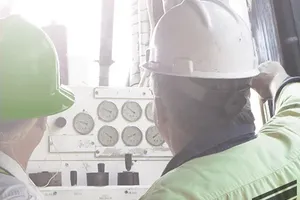
Unsolicited application
Haven't found the right vacancy yet? Send us an unsolicited application!
learn more